Basic Information on Hierarchy of Controls
When assessing the adequacy of existing controls or introducing new controls, a hierarchy of risk controls should be considered. The principles of prevention in the MHSW Regulations are not exactly a hierarchy, but must be considered alongside the usual hierarchy of risk controls, which is as follows:
➤ elimination
➤ substitution
➤ changing work methods/patterns
➤ reduced or limited time exposure
➤ engineering controls (e.g. isolation, insulation and ventilation)
➤ good housekeeping
➤ safe systems of work
➤ training and information
➤ personal protective equipment
➤ welfare
➤ monitoring and supervision
➤ review.
Elimination or substitution
This is the best and most effective way of avoiding a severe hazard and its associated risks. Elimination occurs when a process or activity is totally abandoned because the associated risk is too high.
Substitution describes the use of a less hazardous form of the substance. There are many examples of substitution, such as the use of waterbased rather than oil-based paints, the use of asbestos substitutes and the use of compressed air as a power source rather than electricity. Care must be taken not to introduce additional hazards and risks as a result of a substitution.
Changing work methods/patterns
In some cases it is possible to change the method of working so that exposures are reduced. For example use rods to clear drains instead of strong chemicals; use disposable hooks for holding articles being sprayed instead of exposing people during the cleaning of reusable hooks.
Sometimes the pattern of work can be changed so that people can do things in a more natural way, for example when removing components and packing them consider whether people are right or left handed; encourage people in offi ces to take breaks from computer screens by getting up to photocopy, fetch files or printed documents.
Reduced time exposure
This involves reducing the time during the working day that the employee is exposed to the hazard, either by giving the employee other work or rest periods. It is only suitable for the control of health hazards associated with, for example, noise, display screens and hazardous substances.
However, it is important to note that for many hazards there are short-term exposure limits as well as normal working workplace exposure limits (WELS) over an 8-hour perio. Short term limits must not be exceeded during the reduced time exposure intervals.
Engineering controls
This describes the control of risks by means of engineering design rather than a reliance on preventative actions by the employee. There are several ways of achieving such controls:
1. control the risks at the source (e.g. the use of more efficient dust filters or the purchase of less noisy equipment)
2. control the risk of exposure by:
– isolating the equipment by the use of an enclosure, a barrier or guard
– insulating any electrical or temperature hazard
– ventilate away any hazardous fumes or gases, either naturally or by the use of extractor fans and hoods.
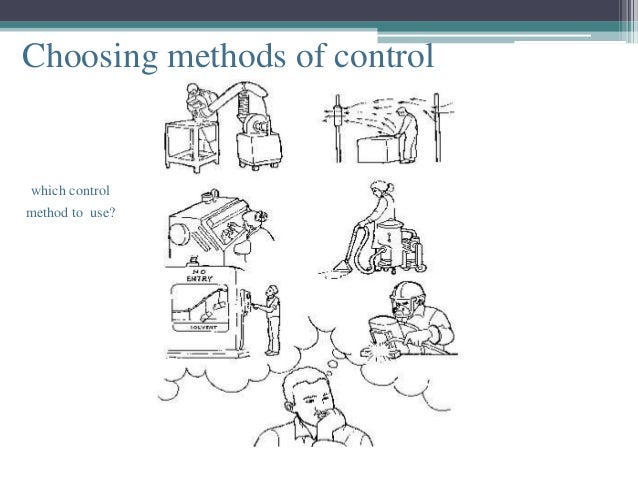
Housekeeping
Housekeeping is a very cheap and effective means of controlling risks. It involves keeping the workplace clean and tidy at all times and maintaining good storage systems for hazardous substances and other potentially dangerous items. The risks most likely to be influenced by good housekeeping are fire and slips, trips and falls.
Safe systems of work
A safe system of work is a requirement of the HSW Act and is dealt with in detail later. The system of work describes the safe method of performing the job activity. If the risks involved are high or medium, the details of the system should be in writing and should be communicated to the employee formally in a training session. Systems for low risk activities may be conveyed verbally. There should be records that the employee (or contractor) has been trained or instructed in the safe system of work and that he or she understands it and will abide by it.
Training and information
Both these topics are important but should not be used in isolation. Information includes such items as signs, posters, systems of work and general health and safety arrangements.
Personal protective equipment
Personal protective equipment (PPE) should only be used as a last resort. There are many reasons for this. The most important limitations are that PPE:
➤ only protects the person wearing the equipment not others nearby
➤ relies on people wearing the equipment at all times
➤ must be used properly
➤ must be replaced when it no longer offers the correct level of protection. This last point is particularly relevant when respiratory protection is used.
The benefits of PPE are:
➤ it gives immediate protection to allow a job to continue while engineering controls are put in place
➤ in an emergency it can be the only practicable way of effecting rescue or shutting down plant in hazardous atmospheres
➤ it can be used to carry out work in confi ned spaces where alternatives are impracticable. But it should never be used to allow people to work in dangerous atmospheres, which are, for example, enriched with oxygen or explosive.
Welfare
Welfare facilities include general workplace ventilation, lighting and heating and the provision of drinking water, sanitation and washing facilities. There is also a requirement to provide eating and rest rooms.
Risk control may be enhanced by the provision of eye washing and shower facilities for use after certain accidents. Within this area of welfare, first aid and health surveillance are important services that should be available.
Monitoring and supervision
All risk control measures, whether they rely on engineered or human behavioural controls, must be monitored for their effectiveness and supervised to ensure that they have been applied correctly. Competent people, who have a sound knowledge of the equipment or process, should undertake monitoring. Checklists are useful to ensure that no significant factor is forgotten.
Any statutory inspection or insurance company reports should be checked to see whether any areas of concern were highlighted and if any recommendations were implemented. Details of any accidents, illnesses or other incidents will give an indication of the effectiveness of the risk control measures. Any emergency arrangements should be tested during the monitoring phase, including first aid provision.
It is crucial that the operator should be monitored to ascertain that all relevant procedures have been understood and followed. The operator may also be able to suggest improvements to the equipment or system of work. The supervisor is an important source of information during the monitoring process.
Where the organization is involved with shift work, it is essential that the risk controls are monitored on all shifts to ensure the uniformity of application. The effectiveness and relevance of any training or instruction given should be monitored.
Review
Periodically the risk control measures should be reviewed. Monitoring and other reports are crucial for the review to be useful. Reviews often take place at safety committee and/or at management meetings. A serious accident or incident should lead to an immediate review of the risk control measures in place.
No comments:
Post a Comment