HAZARDS AND INJURIES OF MANUAL HANDLING AND LIFTING
What are the Hazards and Possible Injuries of Manual Handling?
The term ‘manual handling’ is defined as the movement of a load by human effort alone. This effort may be applied directly or indirectly using a rope or a lever.
Manual handling may involve the transportation of the load or the direct support of the load including pushing, pulling, carrying, moving using bodily force and, of course, straightforward lifting. Back injuries due to the lifting of heavy loads is very common and several million working days are lost each year as a result of such injuries.
Typical hazards of manual handling include:
S lifting a load which is too heavy or too cumbersome resulting in back injury
S poor posture during lifting or poor lifting technique resulting in back injury
S dropping a load, resulting in foot injury
S lifting sharp-edged or hot loads resulting in hand injuries.
Injuries caused by manual handling
Manual handling operations can cause a wide range of acute and chronic injuries to workers. Acute injuries normally lead to sickness leave from work and a period of rest during which time the damage heals.
Chronic injuries build up over a long period of time and are usually irreversible producing illnesses such as arthritic and spinal disorders. There is considerable evidence to suggest that modern life styles, such as a lack of exercise and regular physical effort, have contributed to the long-term serious effects of these injuries.
The most common injuries associated with poor manual handling techniques are all musculoskeletal in nature and are:
S muscular sprains and strains – caused when a muscular tissue (or ligament or tendon) is stretched
beyond its normal capability leading to a weakening, bruising and painful inflammation of the area
affected. Such injuries normally occur in the back or in the arms and wrists
S back injuries – include injuries to the discs situated between the spinal vertebrae (i.e. bones) and can lead to a very painful prolapsed disc lesion (commonly known as a slipped disc). This type of injury can lead to other conditions known as lumbago and sciatica (where pain travels down the leg)
S trapped nerve – usually occurring in the back as a result of another injury but aggravated by manual
handling
S hernia – this is a rupture of the body cavity wall in the lower abdomen causing a protrusion of part of the intestine. This condition eventually requires surgery to repair the damage
S cuts, bruising and abrasions – caused by handling loads with unprotected sharp corners or edges
S fractures – normally of the feet due to the dropping of a load. Fractures of the hand also occur but are less common
S Work-related upper limb disorders (WRULDs)
S rheumatism – this is a chronic disorder involving severe pain in the joints. It has many causes, one of which is believed to be the muscular strains induced by poor manual handling lifting technique.
SAFETY ENGINEERING | ELECTRICAL SAFETY | OSH ELECTRICAL | LIVE WIRE | HIGH VOLTAGE | HUMAN SAFETY
WORKS THAT REQUIRE WORK PERMITS BASIC INFORMATION AND TUTORIALS
WORKS THAT REQUIRES WORK PERMIT
What are the Works that Requires Work Permit?
The main types of permit and the work to be covered by each are identified below.
General permit
The general permit should be used for work such as:
S alterations to or overhaul of plant or machinery where mechanical, toxic or electrical hazards may
arise
S work on or near overhead crane tracks
S work on pipelines with hazardous contents
S work with asbestos-based materials
S work involving ionising radiation
S work at height where there are exceptionally high risks
S excavations to avoid underground services.
Confined space permit
Confined spaces include chambers, tanks (sealed and open-top), vessels, furnaces, ducts, sewers, manholes, pits, flues, excavations, boilers, reactors and ovens.
Many fatal accidents have occurred where inadequate precautions were taken before and during work
involving entry into confined spaces. The two main hazards are the potential presence of toxic or other dangerous substances and the absence of adequate oxygen. In addition, there may be mechanical hazards (entanglement on agitators) and raised temperatures.
The work to be carried out may itself be especially hazardous when done in a confined space, for example, cleaning using solvents, cutting/welding work. Should the person working in a confined space get into difficulties for whatever reason, getting help in and getting the individual out may prove difficult and dangerous.
Stringent preparation, isolation, air testing and other precautions are therefore essential and experience shows that the use of a confined space entry permit is essential to confirm that all the appropriate precautions have been taken.
Work on high voltage apparatus (including testing)
Work on high voltage apparatus (over about 600 volts) is potentially high risk. Hazards include:
S possibly fatal electric shock/burns to the people doing the work
S electrical fires/explosions
S consequential danger from disruption of power supply to safety-critical plant and equipment.
In view of the risk, this work must only be done by suitably trained and competent people acting under the terms of a high voltage permit.
Hot work
Hot work is potentially hazardous as a:
S source of ignition in any plant in which highly flammable materials are handled
S cause of fires in all locations, regardless of whether highly flammable materials are present.
Hot work includes cutting, welding, brazing, soldering and any process involving the application of a naked flame. Drilling and grinding should also be included where a flammable atmosphere is potentially present.
In high risk areas hot work may also involve any equipment or procedure that produces a spark of sufficient energy to ignite highly flammable substances.
Hot work should therefore be done under the terms of a hot work permit, the only exception being where hot work is done in a designated area suitable for the purpose.
What are the Works that Requires Work Permit?
The main types of permit and the work to be covered by each are identified below.
General permit
The general permit should be used for work such as:
S alterations to or overhaul of plant or machinery where mechanical, toxic or electrical hazards may
arise
S work on or near overhead crane tracks
S work on pipelines with hazardous contents
S work with asbestos-based materials
S work involving ionising radiation
S work at height where there are exceptionally high risks
S excavations to avoid underground services.
Confined space permit
Confined spaces include chambers, tanks (sealed and open-top), vessels, furnaces, ducts, sewers, manholes, pits, flues, excavations, boilers, reactors and ovens.
Many fatal accidents have occurred where inadequate precautions were taken before and during work
involving entry into confined spaces. The two main hazards are the potential presence of toxic or other dangerous substances and the absence of adequate oxygen. In addition, there may be mechanical hazards (entanglement on agitators) and raised temperatures.
The work to be carried out may itself be especially hazardous when done in a confined space, for example, cleaning using solvents, cutting/welding work. Should the person working in a confined space get into difficulties for whatever reason, getting help in and getting the individual out may prove difficult and dangerous.
Stringent preparation, isolation, air testing and other precautions are therefore essential and experience shows that the use of a confined space entry permit is essential to confirm that all the appropriate precautions have been taken.
Work on high voltage apparatus (including testing)
Work on high voltage apparatus (over about 600 volts) is potentially high risk. Hazards include:
S possibly fatal electric shock/burns to the people doing the work
S electrical fires/explosions
S consequential danger from disruption of power supply to safety-critical plant and equipment.
In view of the risk, this work must only be done by suitably trained and competent people acting under the terms of a high voltage permit.
Hot work
Hot work is potentially hazardous as a:
S source of ignition in any plant in which highly flammable materials are handled
S cause of fires in all locations, regardless of whether highly flammable materials are present.
Hot work includes cutting, welding, brazing, soldering and any process involving the application of a naked flame. Drilling and grinding should also be included where a flammable atmosphere is potentially present.
In high risk areas hot work may also involve any equipment or procedure that produces a spark of sufficient energy to ignite highly flammable substances.
Hot work should therefore be done under the terms of a hot work permit, the only exception being where hot work is done in a designated area suitable for the purpose.
BIOLOGICAL EFFECTS OF IONIZING RADIATION BASIC INFORMATION AND TUTORIALS
IONIZING RADIATION IMPACT TO BODY
What Are The Biological Effects of Ionizing Radiation?
Information on the biological effects of ionizing radiation comes from animal experiments and from studies of groups of people exposed to relatively high levels of radiation. The best-known groups are the workers in the luminising industry early this century who used to point their brushes with the lips and so ingest radioactivity; the survivors of the atomic bombs dropped on Japan, and patients who have undergone radiotherapy.
Evidence of biological effects is also available from studies of certain miners who inhaled elevated levels of the natural radioactive gas radon and its radioactive decay products. The basic unit of tissue is the cell. Each cell has a nucleus, which may be regarded as its control centre.
Deoxyribonucleic acid (DNA) is the essential component of the cell’s genetic information and makes up the chromosomes which are contained in the nucleus. Although the ways in which radiation damages cells are not fully understood, many involve changes to DNA.
There are two main modes of action. A DNA molecule may become ionised, resulting directly in chemical change, or it may be chemically altered by reaction with agents produced as a result of the ionisation of other cell constituents. The chemical change may ultimately mean that the cell is prevented from further division and can therefore be regarded as dead.
Very high doses of radiation can kill large numbers of cells. If the whole body is exposed, death may occur within a matter of weeks: an instantaneous absorbed dose of 5 gray or more would probably be lethal (the unit gray is defined below).
If a small area of the body is briefly exposed to a very high dose, death may not occur, but there may be other early effects: an instantaneous absorbed dose of 5 gray or more to the skin would probably cause erythema (reddening) in a week or so, and a similar dose to the testes or ovaries might cause sterility.
If the same doses are received in a protracted fashion, there may be no early signs of injury. The effect of very high doses of radiation delivered acutely is used in radiotherapy to destroy malignant tissue. Effects of radiation that only occur above certain levels (i.e. thresholds) are known as deterministic. Above these thresholds, the severity of harm increases with dose.
Low doses or high doses received in a protracted fashion may lead to damage at a later stage. With reproductive cells, the harm is expressed in the irradiated person’s offspring (genetic defects), and may vary from unobservable through mildly detrimental to severely disabling.
So far, however, no genetic defects directly attributable to radiation exposure have been unequivocally observed in human beings. Cancer induction may result from the exposure of a number of different types of a cell. There is always a delay of some years, or even decades, between irradiation and the appearance of a cancer.
It is assumed that within the range of exposure conditions usually encountered in radiation work, the risks of cancer and hereditary damage increase in direct proportion to the radiation dose. It is also assumed that there is no exposure level that is entirely without risk.
Thus, for example, the mortality risk factor for all cancers from uniform radiation of the whole body is now estimated to be 1 in 25 per sievert (see below for definition) for a working population, aged 20 to 64 years, averaged over both sexes5. In scientific notation, this is given as 4 10 2 per sievert.
Effects of radiation, primarily cancer induction, for which there is probably no threshold and the risk is proportional to dose are known as stochastic, meaning ‘of a random or statistical nature’.
What Are The Biological Effects of Ionizing Radiation?
Information on the biological effects of ionizing radiation comes from animal experiments and from studies of groups of people exposed to relatively high levels of radiation. The best-known groups are the workers in the luminising industry early this century who used to point their brushes with the lips and so ingest radioactivity; the survivors of the atomic bombs dropped on Japan, and patients who have undergone radiotherapy.
Evidence of biological effects is also available from studies of certain miners who inhaled elevated levels of the natural radioactive gas radon and its radioactive decay products. The basic unit of tissue is the cell. Each cell has a nucleus, which may be regarded as its control centre.
Deoxyribonucleic acid (DNA) is the essential component of the cell’s genetic information and makes up the chromosomes which are contained in the nucleus. Although the ways in which radiation damages cells are not fully understood, many involve changes to DNA.
There are two main modes of action. A DNA molecule may become ionised, resulting directly in chemical change, or it may be chemically altered by reaction with agents produced as a result of the ionisation of other cell constituents. The chemical change may ultimately mean that the cell is prevented from further division and can therefore be regarded as dead.
Very high doses of radiation can kill large numbers of cells. If the whole body is exposed, death may occur within a matter of weeks: an instantaneous absorbed dose of 5 gray or more would probably be lethal (the unit gray is defined below).
If a small area of the body is briefly exposed to a very high dose, death may not occur, but there may be other early effects: an instantaneous absorbed dose of 5 gray or more to the skin would probably cause erythema (reddening) in a week or so, and a similar dose to the testes or ovaries might cause sterility.
If the same doses are received in a protracted fashion, there may be no early signs of injury. The effect of very high doses of radiation delivered acutely is used in radiotherapy to destroy malignant tissue. Effects of radiation that only occur above certain levels (i.e. thresholds) are known as deterministic. Above these thresholds, the severity of harm increases with dose.
Low doses or high doses received in a protracted fashion may lead to damage at a later stage. With reproductive cells, the harm is expressed in the irradiated person’s offspring (genetic defects), and may vary from unobservable through mildly detrimental to severely disabling.
So far, however, no genetic defects directly attributable to radiation exposure have been unequivocally observed in human beings. Cancer induction may result from the exposure of a number of different types of a cell. There is always a delay of some years, or even decades, between irradiation and the appearance of a cancer.
It is assumed that within the range of exposure conditions usually encountered in radiation work, the risks of cancer and hereditary damage increase in direct proportion to the radiation dose. It is also assumed that there is no exposure level that is entirely without risk.
Thus, for example, the mortality risk factor for all cancers from uniform radiation of the whole body is now estimated to be 1 in 25 per sievert (see below for definition) for a working population, aged 20 to 64 years, averaged over both sexes5. In scientific notation, this is given as 4 10 2 per sievert.
Effects of radiation, primarily cancer induction, for which there is probably no threshold and the risk is proportional to dose are known as stochastic, meaning ‘of a random or statistical nature’.
WORKING ON TRANSFORMERS AND CIRCUIT BREAKERS SAFETY PRECAUTION TIPS AND TUTORIALS
SAFETY PRECAUTIONS ON WORKING ON TRANSFORMERS AND CIRCUIT BREAKERS
What Are The Safety Precautions on Working on Power Transformers and Circuit Breakers
Take the following safety precautions when working on transformers and circuit breakers:
• Prevent moisture from entering when removing covers from oil-filled transformers.
• Do not allow tools, bolts, nuts, or similar objects to drop into the transformers. Tie tools or parts with suitable twine.
• Have workers empty their pockets of lose articles such as knives, keys, and watches.
• Remove all oil from transformer covers, the floor, and the scaffold to eliminate slipping hazards.
• Exhaust gaseous vapor with an air blower before allowing work in large transformer cases because they usually contain some gaseous fumes and are not well ventilated.
• Stay away from the base of the pole or structure while transformers are being raised or lowered.
• Ensure that anyone working on a pole or structure takes a position above or well clear of transformers while the transformers are being raised or supported with blocks.
• Ground the secondary side of a transformer before energizing it except when the transformer is part of an ungrounded delta bank.
• Make an individual secondary-voltage test on all transformers before connecting them to secondary mains. On banks of three transformers connected Y-delta, bring in the primary neutral and leave it connected until the secondary connections have been completed to get a true indication on the lamp tests.
• Disconnect secondary-phase leads before opening primary cutouts when taking a paralleled transformer out of service. Do not disconnect secondary neutral or ground connections until you have opened the primary cutouts.
• Do not stand on top of energized transformers unless absolutely necessary and then only with the permission of the foreman and after all possible precautions have been taken. These precautions include placing a rubber blanket protected with a rubbish bag over the transformer cover. Do not wear climbers.
• Treat the grounded case of a connected transformer the same as any grounded conductor. Treat the ungrounded case of a connected transformer the same as any energized conductor because the case may become energized if transformer windings break down.
• Ensure that the breaker cannot be opened or closed automatically before working on an oil circuit breaker and that it is in the open position or the operating mechanism is blocked.
• Ensure that metal-clad switching equipment is deenergized before working on it.
• Ensure that regulators are off the automatic position and set in the neutral position before doing any switching on a regulated feeder.
• Do not break the charging current of a regulator or large substation transformer by opening disconnect switches because a dangerous arc may result. Use oil or air brake switches unless special instructions to do otherwise have been issued by the proper authority.
• Do not operate outdoor disconnecting switches without using the disconnect pole provided for this
purpose.
• Ensure that all contacts are actually open and that safe clearance is obtained on all three phases each time an air brake switch is opened. Do not depend on the position of the operating handle as evidence that the switch is open.
• Do not operate switches or disconnect switches without proper authority and then only if thoroughly
familiar with the equipment.
• Remove potential transformer fuses with wooden tongs. Wear rubber gloves and leather over gloves.
• Do not open or remove disconnect switches when carrying load. First open the oil circuit breaker in series with the switches. Open disconnect switches slowly and reclose immediately if an arc is drawn.
What Are The Safety Precautions on Working on Power Transformers and Circuit Breakers
Take the following safety precautions when working on transformers and circuit breakers:
• Prevent moisture from entering when removing covers from oil-filled transformers.
• Do not allow tools, bolts, nuts, or similar objects to drop into the transformers. Tie tools or parts with suitable twine.
• Have workers empty their pockets of lose articles such as knives, keys, and watches.
• Remove all oil from transformer covers, the floor, and the scaffold to eliminate slipping hazards.
• Exhaust gaseous vapor with an air blower before allowing work in large transformer cases because they usually contain some gaseous fumes and are not well ventilated.
• Stay away from the base of the pole or structure while transformers are being raised or lowered.
• Ensure that anyone working on a pole or structure takes a position above or well clear of transformers while the transformers are being raised or supported with blocks.
• Ground the secondary side of a transformer before energizing it except when the transformer is part of an ungrounded delta bank.
• Make an individual secondary-voltage test on all transformers before connecting them to secondary mains. On banks of three transformers connected Y-delta, bring in the primary neutral and leave it connected until the secondary connections have been completed to get a true indication on the lamp tests.
• Disconnect secondary-phase leads before opening primary cutouts when taking a paralleled transformer out of service. Do not disconnect secondary neutral or ground connections until you have opened the primary cutouts.
• Do not stand on top of energized transformers unless absolutely necessary and then only with the permission of the foreman and after all possible precautions have been taken. These precautions include placing a rubber blanket protected with a rubbish bag over the transformer cover. Do not wear climbers.
• Treat the grounded case of a connected transformer the same as any grounded conductor. Treat the ungrounded case of a connected transformer the same as any energized conductor because the case may become energized if transformer windings break down.
• Ensure that the breaker cannot be opened or closed automatically before working on an oil circuit breaker and that it is in the open position or the operating mechanism is blocked.
• Ensure that metal-clad switching equipment is deenergized before working on it.
• Ensure that regulators are off the automatic position and set in the neutral position before doing any switching on a regulated feeder.
• Do not break the charging current of a regulator or large substation transformer by opening disconnect switches because a dangerous arc may result. Use oil or air brake switches unless special instructions to do otherwise have been issued by the proper authority.
• Do not operate outdoor disconnecting switches without using the disconnect pole provided for this
purpose.
• Ensure that all contacts are actually open and that safe clearance is obtained on all three phases each time an air brake switch is opened. Do not depend on the position of the operating handle as evidence that the switch is open.
• Do not operate switches or disconnect switches without proper authority and then only if thoroughly
familiar with the equipment.
• Remove potential transformer fuses with wooden tongs. Wear rubber gloves and leather over gloves.
• Do not open or remove disconnect switches when carrying load. First open the oil circuit breaker in series with the switches. Open disconnect switches slowly and reclose immediately if an arc is drawn.
HOTLINE TOOLS SAFETY RULES FOR WORKING BASIC INFORMATION AND TUTORIALS
LINEMAN SAFETY RULES FOR WORKING USING HOTLINE TOOLS
Hotline Tools Safety Rules
Follow these safety rules when working with hot-line tools:
• Do not perform hot-line work when rain or snow is threatening or when heavy dew, fog, or other excessive moisture is present. Exceptions to this rule are when conducting switching operations, fusing, or clearing damaged equipment that presents a hazard to the public or to troops.
• Remain alert. If rain or snow starts to fall or an electrical storm appears while a job is in progress, complete the work as quickly as possible to allow safe, temporary operation of the line until precipitation or lightning ceases. Judgment of safe weather conditions for hot-line work is the foreman's responsibility.
• Perform hot-line work during daylight if possible. In emergency situations, work under artificial light if all conductors and equipment being worked on are made clearly visible.
• Do not wear rubber gloves with hot-line tools because they make detection of brush discharges impossible.
• Avoid holding outer braces or other metal attachments.
• Avoid unnecessary conversation.
• Maintain close cooperation among everyone on the job.
• Treat wooden pole structures the same as steel towers.
• Be careful with distribution primaries. When they are located on the same pole with high-tension lines, cover them with rubber protective equipment before climbing through or working above them.
• Do not change your position on the pole without first looking around and informing others.
• Never use your hands to hold a live line clear of a lineman on a pole. Secure the line with live-line tools and lock it in a clamp.
• Stay below the live wire when moving it until it is thoroughly secured in a safe working position.
Take special precautions on poles having guy lines. Do not use a rope on conductors carrying more than 5,000 volts unless the rope is insulated from the conductor with an insulated tension link stick.
Hotline Tools Safety Rules
Follow these safety rules when working with hot-line tools:
• Do not perform hot-line work when rain or snow is threatening or when heavy dew, fog, or other excessive moisture is present. Exceptions to this rule are when conducting switching operations, fusing, or clearing damaged equipment that presents a hazard to the public or to troops.
• Remain alert. If rain or snow starts to fall or an electrical storm appears while a job is in progress, complete the work as quickly as possible to allow safe, temporary operation of the line until precipitation or lightning ceases. Judgment of safe weather conditions for hot-line work is the foreman's responsibility.
• Perform hot-line work during daylight if possible. In emergency situations, work under artificial light if all conductors and equipment being worked on are made clearly visible.
• Do not wear rubber gloves with hot-line tools because they make detection of brush discharges impossible.
• Avoid holding outer braces or other metal attachments.
• Avoid unnecessary conversation.
• Maintain close cooperation among everyone on the job.
• Treat wooden pole structures the same as steel towers.
• Be careful with distribution primaries. When they are located on the same pole with high-tension lines, cover them with rubber protective equipment before climbing through or working above them.
• Do not change your position on the pole without first looking around and informing others.
• Never use your hands to hold a live line clear of a lineman on a pole. Secure the line with live-line tools and lock it in a clamp.
• Stay below the live wire when moving it until it is thoroughly secured in a safe working position.
Take special precautions on poles having guy lines. Do not use a rope on conductors carrying more than 5,000 volts unless the rope is insulated from the conductor with an insulated tension link stick.
RELATIONSHIP BETWEEN NOISE EXPOSURE AND HEARING LOSS BASIC INFORMATION
WHAT IS THE RELATIONSHIP BETWEEN NOISE EXPOSURE AND HEARING LOSS
The relationship between noise exposure and hearing loss.
If hearing damage is to be prevented by limiting occupational noise exposure, then it is necessary to have some quantitative understanding of the relationships between sound pressure level, frequency, exposure time and the degree of damage caused.
Having established that there is a risk to hearing, though, it would be unethical to refrain from taking all reasonable measures to prevent it. During the 1960s a great deal of work was done in the UK and the rest of the world to establish the relationships between noise exposure and noise-induced hearing loss.
At that time it was relatively easy to find populations who had worked at one job, and been exposed to steady noise levels, for a number of years. Since then, social mobility, changing patterns of employment, and indeed government action to limit noise exposure, have made it much harder to find large groups of workers whose noise exposure can be logged over several years.
Information on the precise relationship between the various factors influencing hearing damage is therefore incomplete, and a full understanding of the subject will never be achieved. Full understanding is not required, though.
What is needed is sufficient information to frame legislation and advisory procedures which are capable of being put into practice in such a way that occupational hearing damage is reduced and eventually eliminated, without also making essential industrial processes impossible or uneconomical to carry out. This is itself quite a demanding objective.
In studying the relationship between noise exposure and hearing loss a range of questions can be asked. It can be assumed that louder sounds will result in more damage than quieter ones, but more detailed questions include:
. Is there a sound pressure level below which there is no contribution to hearing damage?
. If so, then what is this level?
. If all noise contributes to damage then what is the trade-off between level and damage?
. Does an extended period of noise exposure do the same amount of damage as a series of shorter exposures at the same level?
. Are particular frequencies or ranges of frequencies significantly more damaging than others?
. Is there a link between the frequencies to which the ear is exposed and the frequencies at which hearing loss occurs?
The answers to these questions and other questions will all have consequences for the way in which noise exposure must be measured. In the European Union, an approach to the assessment of noise exposure has emerged which uses the best available answers to these questions.
Each of the assumptions listed below can be challenged, and together they represent a gross simplification of a very complicated area of knowledge. For the time being, they seem to offer a practical way forward to those working to reduce occupational hearing loss, and as stated above, that is the most that can be asked for.
1. All sound energy received by the ear will, in some degree, contribute to hearing damage.
2. The degree of damage is proportional to the amount of sound energy deposited in the ear. That means that a doubling of exposure time is equivalent to a 3 dB increase in sound pressure level. It also means that the total exposure time at a given level is important; breaking the overall time up into shorter periods has no effect.
3. The A weighting system correctly evaluates the contribution of different frequencies to hearing loss.
4. Very high sound pressures can cause damage which may not be reflected in an equal-energy assessment as described above. An additional limit on peak sound exposure can be used to prevent this.
In the United States, rather different conclusions have been reached, and as a result a rather different trade-off between sound pressure level and exposure time is used. This is based on the assumption that a 5 dB increase in level (rather than 3 dB) is equivalent to a doubling of exposure time.
To add to the confusion, for some purposes in the United States 4 dB (rather than 3 or 5 dB) is assumed to be equivalent to a doubling of exposure time. Those carrying out noise exposure assessments in Europe need to be aware of these different practices in order to avoid being misled by procedures or instrumentation intended for American use.
The current European approach to the prevention of occupational hearing damage is based on the principles listed above. The issue is the subject of continuing debate as research into hearing damage continues. Given the difficulties of generating further large sets of data which can be used to refine our knowledge, it seems likely that for the foreseeable future this approach will continue.
The relationship between noise exposure and hearing loss.
If hearing damage is to be prevented by limiting occupational noise exposure, then it is necessary to have some quantitative understanding of the relationships between sound pressure level, frequency, exposure time and the degree of damage caused.
Having established that there is a risk to hearing, though, it would be unethical to refrain from taking all reasonable measures to prevent it. During the 1960s a great deal of work was done in the UK and the rest of the world to establish the relationships between noise exposure and noise-induced hearing loss.
At that time it was relatively easy to find populations who had worked at one job, and been exposed to steady noise levels, for a number of years. Since then, social mobility, changing patterns of employment, and indeed government action to limit noise exposure, have made it much harder to find large groups of workers whose noise exposure can be logged over several years.
Information on the precise relationship between the various factors influencing hearing damage is therefore incomplete, and a full understanding of the subject will never be achieved. Full understanding is not required, though.
What is needed is sufficient information to frame legislation and advisory procedures which are capable of being put into practice in such a way that occupational hearing damage is reduced and eventually eliminated, without also making essential industrial processes impossible or uneconomical to carry out. This is itself quite a demanding objective.
In studying the relationship between noise exposure and hearing loss a range of questions can be asked. It can be assumed that louder sounds will result in more damage than quieter ones, but more detailed questions include:
. Is there a sound pressure level below which there is no contribution to hearing damage?
. If so, then what is this level?
. If all noise contributes to damage then what is the trade-off between level and damage?
. Does an extended period of noise exposure do the same amount of damage as a series of shorter exposures at the same level?
. Are particular frequencies or ranges of frequencies significantly more damaging than others?
. Is there a link between the frequencies to which the ear is exposed and the frequencies at which hearing loss occurs?
The answers to these questions and other questions will all have consequences for the way in which noise exposure must be measured. In the European Union, an approach to the assessment of noise exposure has emerged which uses the best available answers to these questions.
Each of the assumptions listed below can be challenged, and together they represent a gross simplification of a very complicated area of knowledge. For the time being, they seem to offer a practical way forward to those working to reduce occupational hearing loss, and as stated above, that is the most that can be asked for.
1. All sound energy received by the ear will, in some degree, contribute to hearing damage.
2. The degree of damage is proportional to the amount of sound energy deposited in the ear. That means that a doubling of exposure time is equivalent to a 3 dB increase in sound pressure level. It also means that the total exposure time at a given level is important; breaking the overall time up into shorter periods has no effect.
3. The A weighting system correctly evaluates the contribution of different frequencies to hearing loss.
4. Very high sound pressures can cause damage which may not be reflected in an equal-energy assessment as described above. An additional limit on peak sound exposure can be used to prevent this.
In the United States, rather different conclusions have been reached, and as a result a rather different trade-off between sound pressure level and exposure time is used. This is based on the assumption that a 5 dB increase in level (rather than 3 dB) is equivalent to a doubling of exposure time.
To add to the confusion, for some purposes in the United States 4 dB (rather than 3 or 5 dB) is assumed to be equivalent to a doubling of exposure time. Those carrying out noise exposure assessments in Europe need to be aware of these different practices in order to avoid being misled by procedures or instrumentation intended for American use.
The current European approach to the prevention of occupational hearing damage is based on the principles listed above. The issue is the subject of continuing debate as research into hearing damage continues. Given the difficulties of generating further large sets of data which can be used to refine our knowledge, it seems likely that for the foreseeable future this approach will continue.
SAFE SYSTEM OF WORK - ADDRESSING ELECTRICAL SAFETY AND WORKPLACE SAFETY
SAFE SYSTEM OF WORK - WHAT YOU NEED TO KNOW
What is Safe System of Work? Basic Tutorials on Safe System of Work
What is a safe system of work?
A safe system of work has been defined as:

The integration of personnel, articles and substances in a laid out and considered method of working which takes proper account of the risks to employees and others who may be affected, such as visitors and contractors, and provides a formal framework to ensure that all of the steps necessary for safe working have been anticipated and implemented.
In simple terms, a safe system of work is a defined method for doing a job in a safe way. It takes account of all foreseeable hazards to health and safety and seeks to eliminate or minimize these. Safe systems of work are normally formal and documented, for example, in written operating procedures but, in some cases, they may be verbal.
The particular importance of safe systems of work stems from the recognition that most accidents are caused by a combination of factors (plant, substances, lack of training, supervision, etc.). Hence prevention must be based on an integral approach and not one which only deals with each factor in isolation.
The adoption of a safe system of work provides this integral approach because an effective safe system:
➤ is based on looking at the job as a whole
➤ starts from an analysis of all foreseeable hazards, e.g. physical, chemical, health;
➤ brings together all the necessary precautions, including design, physical precautions, training, monitoring, procedures and personal protective equipment.
It follows from this that the use of safe systems of work is in no way a replacement for other precautions, such as good equipment design, safe construction and the use of physical safeguards.
However, there are many situations where these will not give adequate protection in themselves, and then a carefully thought-out and properly implemented safe system of work is especially important.
The best example is maintenance and repair work, which will often involve as a fi rst stage dismantling the guard or breaking through the containment, which exists for the protection of the ordinary process operator. In some of these operations, a permit to work procedure will be the most appropriate type of safe system of work. The operations covered may be simple or complex, routine or unusual.
Whether the system is verbal or written, and whether the operation it covers is simple or complex, routine or unusual, the essential features are forethought and planning – to ensure that all foreseeable hazards are iidentified and controlled. In particular, this will involve scrutiny of:
➤ the sequence of operations to be carried out
➤ the equipment, plant, machinery and tools involved
➤ chemicals and other substances to which people might be exposed in the course of the work
➤ the people doing the work – their skill and experience
➤ foreseeable hazards (health, safety, environment), whether to the people doing the work or to others who might be affected by it
➤ practical precautions which, when adopted, will eliminate or minimize these hazards
➤ the training needs of those who will manage and operate under the procedure
➤ monitoring systems to ensure that the defi ned precautions are implemented effectively.
Assessment of what safe systems of work are required
Requirement
It is the responsibility of the management in each organization to ensure that its operations are assessed to determine where safe systems of work need to be developed. This assessment must, at the same time, decide the most appropriate form for the safe system, that is:
\➤ is a written procedure required?
➤ should the operation only be carried out under permit to work?
➤ is an informal system suffi cient?
Factors to be considered for safe systems of work
It is recognized that each organization must have the freedom to devise systems that match the risk potential of their operations and which are practicable in their situation.
However, they should take account of the following factors in making their decision:
➤ types of risk involved in the operation
➤ magnitude of the risk, including consideration of the worst foreseeable loss
➤ complexity of the operation
➤ past accident and loss experience
➤ requirements and recommendations of the relevant health and safety authorities
➤ the type of documentation needed
➤ resources required to implement the safe system of work (including training and monitoring).
What is Safe System of Work? Basic Tutorials on Safe System of Work
What is a safe system of work?
A safe system of work has been defined as:

The integration of personnel, articles and substances in a laid out and considered method of working which takes proper account of the risks to employees and others who may be affected, such as visitors and contractors, and provides a formal framework to ensure that all of the steps necessary for safe working have been anticipated and implemented.
In simple terms, a safe system of work is a defined method for doing a job in a safe way. It takes account of all foreseeable hazards to health and safety and seeks to eliminate or minimize these. Safe systems of work are normally formal and documented, for example, in written operating procedures but, in some cases, they may be verbal.
The particular importance of safe systems of work stems from the recognition that most accidents are caused by a combination of factors (plant, substances, lack of training, supervision, etc.). Hence prevention must be based on an integral approach and not one which only deals with each factor in isolation.
The adoption of a safe system of work provides this integral approach because an effective safe system:
➤ is based on looking at the job as a whole
➤ starts from an analysis of all foreseeable hazards, e.g. physical, chemical, health;
➤ brings together all the necessary precautions, including design, physical precautions, training, monitoring, procedures and personal protective equipment.
It follows from this that the use of safe systems of work is in no way a replacement for other precautions, such as good equipment design, safe construction and the use of physical safeguards.
However, there are many situations where these will not give adequate protection in themselves, and then a carefully thought-out and properly implemented safe system of work is especially important.
The best example is maintenance and repair work, which will often involve as a fi rst stage dismantling the guard or breaking through the containment, which exists for the protection of the ordinary process operator. In some of these operations, a permit to work procedure will be the most appropriate type of safe system of work. The operations covered may be simple or complex, routine or unusual.
Whether the system is verbal or written, and whether the operation it covers is simple or complex, routine or unusual, the essential features are forethought and planning – to ensure that all foreseeable hazards are iidentified and controlled. In particular, this will involve scrutiny of:
➤ the sequence of operations to be carried out
➤ the equipment, plant, machinery and tools involved
➤ chemicals and other substances to which people might be exposed in the course of the work
➤ the people doing the work – their skill and experience
➤ foreseeable hazards (health, safety, environment), whether to the people doing the work or to others who might be affected by it
➤ practical precautions which, when adopted, will eliminate or minimize these hazards
➤ the training needs of those who will manage and operate under the procedure
➤ monitoring systems to ensure that the defi ned precautions are implemented effectively.
Assessment of what safe systems of work are required
Requirement
It is the responsibility of the management in each organization to ensure that its operations are assessed to determine where safe systems of work need to be developed. This assessment must, at the same time, decide the most appropriate form for the safe system, that is:
\➤ is a written procedure required?
➤ should the operation only be carried out under permit to work?
➤ is an informal system suffi cient?
Factors to be considered for safe systems of work
It is recognized that each organization must have the freedom to devise systems that match the risk potential of their operations and which are practicable in their situation.
However, they should take account of the following factors in making their decision:
➤ types of risk involved in the operation
➤ magnitude of the risk, including consideration of the worst foreseeable loss
➤ complexity of the operation
➤ past accident and loss experience
➤ requirements and recommendations of the relevant health and safety authorities
➤ the type of documentation needed
➤ resources required to implement the safe system of work (including training and monitoring).
HIERARCHY OF RISK CONTROLS FOR ELECTRICAL SAFETY AND WORKPLACE
Basic Information on Hierarchy of Controls
When assessing the adequacy of existing controls or introducing new controls, a hierarchy of risk controls should be considered. The principles of prevention in the MHSW Regulations are not exactly a hierarchy, but must be considered alongside the usual hierarchy of risk controls, which is as follows:
➤ elimination
➤ substitution
➤ changing work methods/patterns
➤ reduced or limited time exposure
➤ engineering controls (e.g. isolation, insulation and ventilation)
➤ good housekeeping
➤ safe systems of work
➤ training and information
➤ personal protective equipment
➤ welfare
➤ monitoring and supervision
➤ review.
Elimination or substitution
This is the best and most effective way of avoiding a severe hazard and its associated risks. Elimination occurs when a process or activity is totally abandoned because the associated risk is too high.
Substitution describes the use of a less hazardous form of the substance. There are many examples of substitution, such as the use of waterbased rather than oil-based paints, the use of asbestos substitutes and the use of compressed air as a power source rather than electricity. Care must be taken not to introduce additional hazards and risks as a result of a substitution.
Changing work methods/patterns
In some cases it is possible to change the method of working so that exposures are reduced. For example use rods to clear drains instead of strong chemicals; use disposable hooks for holding articles being sprayed instead of exposing people during the cleaning of reusable hooks.
Sometimes the pattern of work can be changed so that people can do things in a more natural way, for example when removing components and packing them consider whether people are right or left handed; encourage people in offi ces to take breaks from computer screens by getting up to photocopy, fetch files or printed documents.
Reduced time exposure
This involves reducing the time during the working day that the employee is exposed to the hazard, either by giving the employee other work or rest periods. It is only suitable for the control of health hazards associated with, for example, noise, display screens and hazardous substances.
However, it is important to note that for many hazards there are short-term exposure limits as well as normal working workplace exposure limits (WELS) over an 8-hour perio. Short term limits must not be exceeded during the reduced time exposure intervals.
Engineering controls
This describes the control of risks by means of engineering design rather than a reliance on preventative actions by the employee. There are several ways of achieving such controls:
1. control the risks at the source (e.g. the use of more efficient dust filters or the purchase of less noisy equipment)
2. control the risk of exposure by:
– isolating the equipment by the use of an enclosure, a barrier or guard
– insulating any electrical or temperature hazard
– ventilate away any hazardous fumes or gases, either naturally or by the use of extractor fans and hoods.
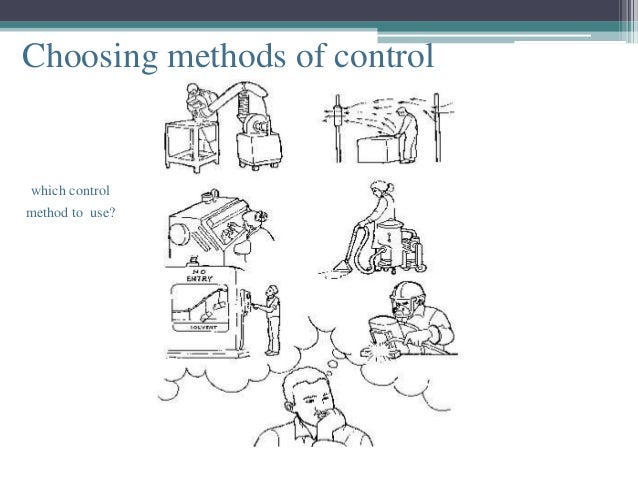
Housekeeping
Housekeeping is a very cheap and effective means of controlling risks. It involves keeping the workplace clean and tidy at all times and maintaining good storage systems for hazardous substances and other potentially dangerous items. The risks most likely to be influenced by good housekeeping are fire and slips, trips and falls.
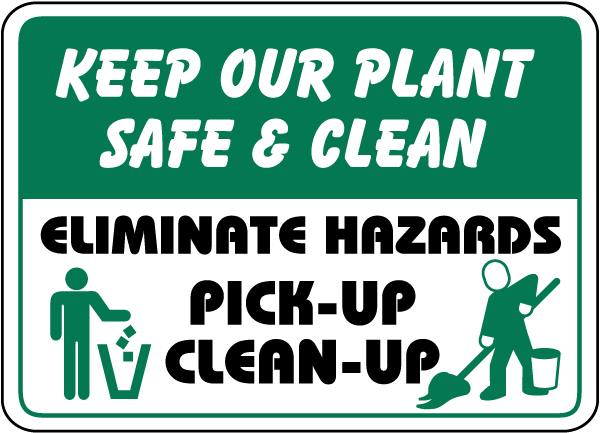
Safe systems of work
A safe system of work is a requirement of the HSW Act and is dealt with in detail later. The system of work describes the safe method of performing the job activity. If the risks involved are high or medium, the details of the system should be in writing and should be communicated to the employee formally in a training session. Systems for low risk activities may be conveyed verbally. There should be records that the employee (or contractor) has been trained or instructed in the safe system of work and that he or she understands it and will abide by it.
Training and information
Both these topics are important but should not be used in isolation. Information includes such items as signs, posters, systems of work and general health and safety arrangements.
Personal protective equipment
Personal protective equipment (PPE) should only be used as a last resort. There are many reasons for this. The most important limitations are that PPE:

➤ only protects the person wearing the equipment not others nearby
➤ relies on people wearing the equipment at all times
➤ must be used properly
➤ must be replaced when it no longer offers the correct level of protection. This last point is particularly relevant when respiratory protection is used.
The benefits of PPE are:
➤ it gives immediate protection to allow a job to continue while engineering controls are put in place
➤ in an emergency it can be the only practicable way of effecting rescue or shutting down plant in hazardous atmospheres
➤ it can be used to carry out work in confi ned spaces where alternatives are impracticable. But it should never be used to allow people to work in dangerous atmospheres, which are, for example, enriched with oxygen or explosive.
Welfare
Welfare facilities include general workplace ventilation, lighting and heating and the provision of drinking water, sanitation and washing facilities. There is also a requirement to provide eating and rest rooms.
Risk control may be enhanced by the provision of eye washing and shower facilities for use after certain accidents. Within this area of welfare, first aid and health surveillance are important services that should be available.
Monitoring and supervision
All risk control measures, whether they rely on engineered or human behavioural controls, must be monitored for their effectiveness and supervised to ensure that they have been applied correctly. Competent people, who have a sound knowledge of the equipment or process, should undertake monitoring. Checklists are useful to ensure that no significant factor is forgotten.
Any statutory inspection or insurance company reports should be checked to see whether any areas of concern were highlighted and if any recommendations were implemented. Details of any accidents, illnesses or other incidents will give an indication of the effectiveness of the risk control measures. Any emergency arrangements should be tested during the monitoring phase, including first aid provision.
It is crucial that the operator should be monitored to ascertain that all relevant procedures have been understood and followed. The operator may also be able to suggest improvements to the equipment or system of work. The supervisor is an important source of information during the monitoring process.
Where the organization is involved with shift work, it is essential that the risk controls are monitored on all shifts to ensure the uniformity of application. The effectiveness and relevance of any training or instruction given should be monitored.
Review
Periodically the risk control measures should be reviewed. Monitoring and other reports are crucial for the review to be useful. Reviews often take place at safety committee and/or at management meetings. A serious accident or incident should lead to an immediate review of the risk control measures in place.
ELECTRICAL HAZARDS GENERAL CONTROL MEASURES BASIC INFORMATION AND TUTORIALS
General control measures for electrical hazards

The principal control measures for electrical hazards are contained in the statutory precautionary requirements covered by the Electricity at Work Regulations. They are applicable to all electrical equipment and systems found at the workplace and impose duties on employers, employees and the self-employed.
The regulations cover the following topics:
S the design, construction and maintenance of electrical systems, work activities and protective
equipment
S the strength and capability of electrical equipment
S the protection of equipment against adverse and hazardous environments
S the insulation, protection and placing of electrical conductors
S the earthing of conductors and other suitable precautions
S the integrity of referenced conductors
S the suitability of joints and connections used in electrical systems
S means for protection from excess current
S means for cutting off the supply and for isolation
S the precautions to be taken for work on equipment made dead
S working on or near live conductors
S adequate working space, access and lighting
S the competence requirements for persons working on electrical equipment to prevent danger and injury.

Detailed safety standards for designers and installers of electrical systems and equipment are given a code of practice published by the Institution of Electrical Engineers, known as the IEE Regulations. While these regulations are not legally binding, they are recognized as a code of good practice and widely used as an industry standard.
The risk of injury and damage inherent in the use of electricity can only be controlled effectively by the introduction of employee training, safe operating procedures (safe systems of work) and guidance to cover specific tasks.
Training is required at all levels of the organization ranging from simple on-the-job instruction to apprenticeship for electrical technicians and supervisory courses for experienced electrical engineers. First aid training related to the need for cardiovascular resuscitation and treatment of electric burns should be available to all people working on electrical equipment and their supervisors.
A management system should be in place to ensure that the electrical systems are installed, operated and maintained in a safe manner. All managers should be responsible for the provision of adequate resources of people, material and advice to ensure that the safety of electrical systems under their control is satisfactory and that safe systems of work are in place for all electrical equipment
For small factories and office or shop premises where the system voltages are normally at mains voltage, it may be necessary for an external competent person to be available to offer the necessary advice.

Managers must set up a high voltage permit-to-work system for all work at and above 600 volts. The system should be appropriate to the extent of the electrical system involved. Consideration should also be given to the introduction of a permit system for voltages under 600 volts when appropriate and for all work on live conductors.
The additional control measures that should be taken when working with electrical or using electrical equipment are summarized by the following topics:
S the selection of suitable equipment
S the use of protective systems
S inspection and maintenance strategies

The principal control measures for electrical hazards are contained in the statutory precautionary requirements covered by the Electricity at Work Regulations. They are applicable to all electrical equipment and systems found at the workplace and impose duties on employers, employees and the self-employed.
The regulations cover the following topics:
S the design, construction and maintenance of electrical systems, work activities and protective
equipment
S the strength and capability of electrical equipment
S the protection of equipment against adverse and hazardous environments
S the insulation, protection and placing of electrical conductors
S the earthing of conductors and other suitable precautions
S the integrity of referenced conductors
S the suitability of joints and connections used in electrical systems
S means for protection from excess current
S means for cutting off the supply and for isolation
S the precautions to be taken for work on equipment made dead
S working on or near live conductors
S adequate working space, access and lighting
S the competence requirements for persons working on electrical equipment to prevent danger and injury.

Detailed safety standards for designers and installers of electrical systems and equipment are given a code of practice published by the Institution of Electrical Engineers, known as the IEE Regulations. While these regulations are not legally binding, they are recognized as a code of good practice and widely used as an industry standard.
The risk of injury and damage inherent in the use of electricity can only be controlled effectively by the introduction of employee training, safe operating procedures (safe systems of work) and guidance to cover specific tasks.
Training is required at all levels of the organization ranging from simple on-the-job instruction to apprenticeship for electrical technicians and supervisory courses for experienced electrical engineers. First aid training related to the need for cardiovascular resuscitation and treatment of electric burns should be available to all people working on electrical equipment and their supervisors.
A management system should be in place to ensure that the electrical systems are installed, operated and maintained in a safe manner. All managers should be responsible for the provision of adequate resources of people, material and advice to ensure that the safety of electrical systems under their control is satisfactory and that safe systems of work are in place for all electrical equipment
For small factories and office or shop premises where the system voltages are normally at mains voltage, it may be necessary for an external competent person to be available to offer the necessary advice.
Managers must set up a high voltage permit-to-work system for all work at and above 600 volts. The system should be appropriate to the extent of the electrical system involved. Consideration should also be given to the introduction of a permit system for voltages under 600 volts when appropriate and for all work on live conductors.
The additional control measures that should be taken when working with electrical or using electrical equipment are summarized by the following topics:
S the selection of suitable equipment
S the use of protective systems
S inspection and maintenance strategies
SAFETY MONITORING SYSTEM THAT YOU CAN PUT IN PLACE TO DEVELOP SAFETY AWARENESS
SAFETY MONITORING SYSTEM
Safety monitoring is concerned with the measurement and evaluation of safety performance. It may take the following forms:
1. Safety surveys: This is a detailed examination of a number of critical areas of operation or, perhaps, an in-depth study of all health and safety related activities in a workplace.
2. Safety tours: These are an unscheduled examination of a working area, frequently undertaken as a group exercise (eg foreman, safety representative and safety committee member), to assess general compliance with safety requirements (eg fire protection measures and use of machinery safety devices).
3. Safety audits: A safety audit fundamentally subjects each area of an organisation’s activities to a systematic critical examination with the object of minimising injury and loss. It generally takes the form of a series of questions directed to examining factors such as the operation of safe systems of work, compliance with the Statement of Health and Safety Policy and the operation of hazard reporting systems.
4. Safety inspections: A scheduled inspection of a premises or working area to assess levels of legal compliance and observation of company safety procedures. Safety inspections are frequently undertaken by company safety specialists and trade union safety representatives.
5. Safety sampling: A system designed to measure by random sampling the accident potential in a workplace or process by identifying defects in safety performance or omissions. Observers follow a prescribed route through the working area noting deficiencies in performance, eg concerning the wearing of personal protective equipment or the use of correct manual handling techniques.
In some cases, individual topics in the safety sampling exercise are ranked according to importance with a maximum number of points achievable. At the end of the exercise a total score is identified which gives an indication of the performance level at that point in time.
6. Hazard and operability studies: Such studies incorporate the application of formal critical examination to the process and engineering intentions regarding new facilities. The principal aim of such a study is to assess the hazard potential arising from the incorrect operation of equipment and the consequential effects on the facility. Such an operation enables remedial action to be taken at a very early stage.
7. Damage control: Levels of damage are an indication of future accident potential. Damage control operates on the philosophy that non-injury accidents are just as important as injury accidents. The elimination of the causes of accidents resulting in damage to property, plant and products frequently results in a reduction in injury accidents.
Safety monitoring is concerned with the measurement and evaluation of safety performance. It may take the following forms:
1. Safety surveys: This is a detailed examination of a number of critical areas of operation or, perhaps, an in-depth study of all health and safety related activities in a workplace.
2. Safety tours: These are an unscheduled examination of a working area, frequently undertaken as a group exercise (eg foreman, safety representative and safety committee member), to assess general compliance with safety requirements (eg fire protection measures and use of machinery safety devices).
3. Safety audits: A safety audit fundamentally subjects each area of an organisation’s activities to a systematic critical examination with the object of minimising injury and loss. It generally takes the form of a series of questions directed to examining factors such as the operation of safe systems of work, compliance with the Statement of Health and Safety Policy and the operation of hazard reporting systems.
4. Safety inspections: A scheduled inspection of a premises or working area to assess levels of legal compliance and observation of company safety procedures. Safety inspections are frequently undertaken by company safety specialists and trade union safety representatives.
5. Safety sampling: A system designed to measure by random sampling the accident potential in a workplace or process by identifying defects in safety performance or omissions. Observers follow a prescribed route through the working area noting deficiencies in performance, eg concerning the wearing of personal protective equipment or the use of correct manual handling techniques.
In some cases, individual topics in the safety sampling exercise are ranked according to importance with a maximum number of points achievable. At the end of the exercise a total score is identified which gives an indication of the performance level at that point in time.
6. Hazard and operability studies: Such studies incorporate the application of formal critical examination to the process and engineering intentions regarding new facilities. The principal aim of such a study is to assess the hazard potential arising from the incorrect operation of equipment and the consequential effects on the facility. Such an operation enables remedial action to be taken at a very early stage.
7. Damage control: Levels of damage are an indication of future accident potential. Damage control operates on the philosophy that non-injury accidents are just as important as injury accidents. The elimination of the causes of accidents resulting in damage to property, plant and products frequently results in a reduction in injury accidents.
ACCIDENT PREVENTION STRATEGIES FOR AND BY MANAGERS AND SUPERVISORS
MEANS OF ACCIDENT PREVENTION THAT CAN BE INITIATED BY MANAGERS
As a Manager, there are means and ways that can prevent accidents that you may initiate.
Means of preventing accidents
Strategies for preventing accidents take many forms. These include:
1. Prohibition: Some processes and practices may be so inherently dangerous that the only way to prevent accidents is by management placing a total prohibition on that activity. This may take the form of a prohibition on the use of a particular substance, such as an identified toxic substance, or of prohibiting people from carrying out unsafe practices, such as riding on the tines of a fork-lift truck, climbing over moving conveyors or working on roofs without crawlboards.
2. Substitution: The substitution of a less dangerous material or system of work will, in many cases, reduce accident potential. Typical examples are the introduction of remote control handling facilities for direct manual handling operations, the substitution of toluene, a much safer substance, for benzene, and the use of non-asbestos substitutes for boiler and pipe lagging.
3. Change of process: Design or process engineering can usually change a process to ensure better operator protection. Safety aspects of new systems should be considered in the early stages of projects.
4. Process control: This can be achieved through the isolation of a particular process, the use of ‘permit to work’ systems, mechanical or remote control handling systems, restriction of certain operations to highly trained and competent operators, and the introduction of dust and fume arrestment plant.
5. Safe systems of work: Formally designated safe systems of work, with high levels of training, supervision and control, are an important strategy in accident prevention (see below).
6. Personal protective equipment: This entails the provision of items such as safety boots, goggles, aprons, gloves, etc, but is limited in its application as a safety strategy

Safe systems of work
A safe system of work is defined as ‘the integration of men, machinery and materials in the correct environment to provide the safest possible working conditions in a particular working area’.
A safe system of work should incorporate the following features:
(a) a correct sequence of operations;
(b) a safe working area layout;
(c) a controlled environment in terms of temperature, lighting, ventilation, dust control, humidity control, sound pressure levels and radiation hazards; and
(d) clear specification of safe practices and procedures for the task in question.
Safe systems of work are generally designed through the technique of ‘job safety analysis’.
Subscribe to:
Posts (Atom)