Statistics on accidental electrocution show that quite a few of them involve work on or near overhead electric lines. Work on overhead lines is only to be done by qualified electrical lineworkers.
Many times, due to the need to maintain service continuity, the lines are kept energized while work is being performed on them. Lineworkers must be well trained to perform such tasks using safe practices, appropriate personal protective equipment, and insulated tools.
When planning for work on overhead lines, however, one should always try to make the safest choice, which is to put the lines in an electrically safe work condition. Grounding the lines to create an equipotential zone within which a lineworker can be safe is advisable while working on overhead lines.
Work on or near overhead lines requires unique safety analysis because
a) The overhead lines can change position due to wind or other disturbances.
b) A person working on the lines is not usually in the most stable position.
c) The voltages and energy levels involved with overhead lines are often large.
Working near overhead lines, or near vehicles and equipment that could contact overhead lines, requires electrical safety training even for nonelectrical personnel.
The National Electrical Safety Code¨ (NESC¨) (Accredited Standards Committee C2-1997) is a key document that gives significant detail regarding the safety rules for the installation and maintenance of overhead electric supply and communication lines. NFPA 70E-1995 also mentions safety around overhead lines in Part II.
The OSHA regulations that cover work on and near overhead electric lines are 29 CFR 1910.269 and 29 CFR 1910.333 for general industry, and 29 CFR 1926.955 for the construction industry.
SAFETY ENGINEERING | ELECTRICAL SAFETY | OSH ELECTRICAL | LIVE WIRE | HIGH VOLTAGE | HUMAN SAFETY
TEMPORARY PERSONAL PROTECTIVE GROUNDING BASICS
What is temporary personal protective grounding?
Sometimes, additional measures are desirable to provide an extra margin of safety assurance. Temporary personal protective grounds are used when working on de-energized electrical conductors to minimize the possibility of accidental re-energization from unexpected sources. Sometimes these are called safety grounds or equipotential grounding.
Induced voltages, capacitive recharging, and accidental contact with other circuits can occur. Depending on the electrical energy available, these occurrences could cause injury or death.
More often, however, they only cause reßexive actions. For example, although most induced voltages will not normally cause serious injury themselves, they could cause a person to jump backward suddenly, possibly tripping against something or falling to the floor.
Temporary protective grounding devices should be applied where such conditions might occur. Temporary personal protective grounds should be applied at possible points of re-energization. They can also be applied in such a way as to establish a zone of equipotential around a person.
When these grounds are used, they shall be connected tightly, since they establish a deliberate fault point in the circuit. If current does somehow get onto the circuit, the grounds shall stay connected securely until a protective device clears the circuit.
It is difficult to set firm criteria for when temporary personal protective grounds are needed. Blanket requirements are usually established. Many times, it is a decision made in the field by the person performing the work.
When there is uncertainty about exposure, it is wise to add this extra protection. Many industrial facilities and utilities require temporary personal protective grounding for all aerial power line work and for all work on power systems over 600 V because of the increased exposure these systems often have due to their length and location.
Temporary personal protective grounding can also be used as the additional safety measure required when hazardous electrical energy control must be performed using a tag only. Temporary personal protective grounding devices should meet the specifications in ASTM F855-96 and should be sized for the maximum available current of any possible event.
Temporary personal protective grounds should only be installed after all other conditions of an electrically safe work condition have been established. Because the unexpected can happen at any time, however, the installation and removal of temporary grounding devices should be performed, by procedure, as the conductors are energized.
When installed inside equipment enclosures, temporary grounds should be lengthy enough to extend outside of the equipment so that they can be easily seen. If they cannot extend out, they should be made highly visible. Brightly colored tapes are helpful identifiers. Once they are installed, bare-hand work could be permitted.
It should be quite obvious that all personal protective grounds must be removed prior to reenergization. Identification and accountability controls may be necessary on large construction or maintenance jobs. The installation and removal of these grounding devices can be controlled by permit in order to avoid re-energizing equipment into a faulted condition.
The integrity of personal protective grounds should be maintained through the use of periodic inspection and testing. It is a good idea to document this inspection and testing.
Sometimes, additional measures are desirable to provide an extra margin of safety assurance. Temporary personal protective grounds are used when working on de-energized electrical conductors to minimize the possibility of accidental re-energization from unexpected sources. Sometimes these are called safety grounds or equipotential grounding.
Induced voltages, capacitive recharging, and accidental contact with other circuits can occur. Depending on the electrical energy available, these occurrences could cause injury or death.
More often, however, they only cause reßexive actions. For example, although most induced voltages will not normally cause serious injury themselves, they could cause a person to jump backward suddenly, possibly tripping against something or falling to the floor.
Temporary protective grounding devices should be applied where such conditions might occur. Temporary personal protective grounds should be applied at possible points of re-energization. They can also be applied in such a way as to establish a zone of equipotential around a person.
When these grounds are used, they shall be connected tightly, since they establish a deliberate fault point in the circuit. If current does somehow get onto the circuit, the grounds shall stay connected securely until a protective device clears the circuit.
It is difficult to set firm criteria for when temporary personal protective grounds are needed. Blanket requirements are usually established. Many times, it is a decision made in the field by the person performing the work.
When there is uncertainty about exposure, it is wise to add this extra protection. Many industrial facilities and utilities require temporary personal protective grounding for all aerial power line work and for all work on power systems over 600 V because of the increased exposure these systems often have due to their length and location.
Temporary personal protective grounding can also be used as the additional safety measure required when hazardous electrical energy control must be performed using a tag only. Temporary personal protective grounding devices should meet the specifications in ASTM F855-96 and should be sized for the maximum available current of any possible event.
Temporary personal protective grounds should only be installed after all other conditions of an electrically safe work condition have been established. Because the unexpected can happen at any time, however, the installation and removal of temporary grounding devices should be performed, by procedure, as the conductors are energized.
When installed inside equipment enclosures, temporary grounds should be lengthy enough to extend outside of the equipment so that they can be easily seen. If they cannot extend out, they should be made highly visible. Brightly colored tapes are helpful identifiers. Once they are installed, bare-hand work could be permitted.
It should be quite obvious that all personal protective grounds must be removed prior to reenergization. Identification and accountability controls may be necessary on large construction or maintenance jobs. The installation and removal of these grounding devices can be controlled by permit in order to avoid re-energizing equipment into a faulted condition.
The integrity of personal protective grounds should be maintained through the use of periodic inspection and testing. It is a good idea to document this inspection and testing.
POOR HAZARDOUS ELECTRICAL ENERGY CONTROL PRACTICES
What are the examples of poor hazardous energy control practices.
The following items discuss some practices that were used in the past for safety control. These practices are not truly safe practices and should not be used today.
a) Locking out a push-button, control switch, or other pilot device does not ensure that the circuit will remain de-energized. A short circuit or ground in the control circuit can bypass the pilot device.
Another employee might even engage the contactor or starter by hand. Unless the disconnecting means is opened and locked out, an employee should not place himself in a position where unexpected equipment startup or energization might cause injury.
b) Turning the handle of a disconnect switch to the "off' position does not ensure safety. The switch linkage might be broken, leaving the switchblades engaged.
Switchblades in the open position should be confirmed by visual inspection. The load side of the switch should also be checked with a voltage tester to ensure that the outgoing circuit is de-energized, and that there is no backfeed.
c) Removing and tagging fuses does not constitute a lockout/tagout. A lockout/tagout device should be attached to the fuse clips in a manner such that no fuses can be inserted without removing the device.
If fuses are contained in a drawout fuse block, the tag should be attached to the fuse panel, not to the drawout block. Special precautions shall be taken to prevent shock whenever energized fuse clips that are accessible to the touch must be tagged.
d) Simply opening a power circuit breaker does not ensure safety. Even if the control fuses are removed, the breaker can still be engaged with the manual operating mechanism.
The switchgear must be racked away from the bus contacts and into the "fully disconnected" position, and the racking mechanism shall be locked and tagged.
The following items discuss some practices that were used in the past for safety control. These practices are not truly safe practices and should not be used today.
a) Locking out a push-button, control switch, or other pilot device does not ensure that the circuit will remain de-energized. A short circuit or ground in the control circuit can bypass the pilot device.
Another employee might even engage the contactor or starter by hand. Unless the disconnecting means is opened and locked out, an employee should not place himself in a position where unexpected equipment startup or energization might cause injury.
b) Turning the handle of a disconnect switch to the "off' position does not ensure safety. The switch linkage might be broken, leaving the switchblades engaged.
Switchblades in the open position should be confirmed by visual inspection. The load side of the switch should also be checked with a voltage tester to ensure that the outgoing circuit is de-energized, and that there is no backfeed.
c) Removing and tagging fuses does not constitute a lockout/tagout. A lockout/tagout device should be attached to the fuse clips in a manner such that no fuses can be inserted without removing the device.
If fuses are contained in a drawout fuse block, the tag should be attached to the fuse panel, not to the drawout block. Special precautions shall be taken to prevent shock whenever energized fuse clips that are accessible to the touch must be tagged.
d) Simply opening a power circuit breaker does not ensure safety. Even if the control fuses are removed, the breaker can still be engaged with the manual operating mechanism.
The switchgear must be racked away from the bus contacts and into the "fully disconnected" position, and the racking mechanism shall be locked and tagged.
LOCK OUT AND TAG OUT PERMIT BASIC INFORMATION
Some work requires rigid lockout/tagout control of the type that should not be the responsibility of the employee alone. Lockout/tagouts of this nature should be secured by a formal permit.
This more formal approach is called a documented lockout/tagout. Typically, this type of lockout/tagout would be used on those types of jobs that are not simple and easily understood.
Electrical work performed on medium- and high-voltage circuits is a good example. It would also include work on equipment that requires a complex lockout/tagout due to multiple sources of electrical energy.
Also included would be jobs that require work inside of grinding mills, choppers, fan housings, ovens, storage tanks and silos, and similar situations in which personnel are in a position that unexpected equipment start-up would, without question, result in serious injury or death.
In general, the documented lockout/tagout shall be used except when the conditions given in 29 CFR 1910.147 for a nondocumented lockout/tagout allow an exception.
No specific permit system can be recommended as good practice in all circumstances. A workable permit system can be developed only on an individual basis at the plant level by personnel intimately familiar with plant operations. Certain requirements that represent good practice in one plant might be inadequate or unworkable in another plant with different problems and a different personnel structure.
One fundamental feature, however, should be incorporated into any permit system. It should be designed with checks and balances.
Specific responsibility for a particular operation should be assigned to an individual without relieving others of the obligation to double-check the status of the lockout/tagout before proceeding with their own assigned steps in the process. The permit system, then, should be developed to duplicate and reinforce, rather than dilute, responsibility.
Every step in processing a lockout/tagout permit, from the initial request to the official closing, should be confirmed in writing on an official form. The permit form should include spaces for every person involved to indicate the times and dates when the paperwork was received and when the action was taken.
Completion of each step should be acknowledged by the signature of the person responsible for taking the appropriate action. Every person involved in processing the permit should be held responsible for checking the paperwork referred to them to see that everything is in order before proceeding with their own step.
This more formal approach is called a documented lockout/tagout. Typically, this type of lockout/tagout would be used on those types of jobs that are not simple and easily understood.
Electrical work performed on medium- and high-voltage circuits is a good example. It would also include work on equipment that requires a complex lockout/tagout due to multiple sources of electrical energy.
Also included would be jobs that require work inside of grinding mills, choppers, fan housings, ovens, storage tanks and silos, and similar situations in which personnel are in a position that unexpected equipment start-up would, without question, result in serious injury or death.
In general, the documented lockout/tagout shall be used except when the conditions given in 29 CFR 1910.147 for a nondocumented lockout/tagout allow an exception.
No specific permit system can be recommended as good practice in all circumstances. A workable permit system can be developed only on an individual basis at the plant level by personnel intimately familiar with plant operations. Certain requirements that represent good practice in one plant might be inadequate or unworkable in another plant with different problems and a different personnel structure.
One fundamental feature, however, should be incorporated into any permit system. It should be designed with checks and balances.
Specific responsibility for a particular operation should be assigned to an individual without relieving others of the obligation to double-check the status of the lockout/tagout before proceeding with their own assigned steps in the process. The permit system, then, should be developed to duplicate and reinforce, rather than dilute, responsibility.
Every step in processing a lockout/tagout permit, from the initial request to the official closing, should be confirmed in writing on an official form. The permit form should include spaces for every person involved to indicate the times and dates when the paperwork was received and when the action was taken.
Completion of each step should be acknowledged by the signature of the person responsible for taking the appropriate action. Every person involved in processing the permit should be held responsible for checking the paperwork referred to them to see that everything is in order before proceeding with their own step.
SAFE MAINTENANCE PRE PLAN FOR ELECTRICAL FACILITIES BASIC INFORMATION
The design of a facility and its electrical equipment should include consideration for future maintenance. In order to remain in good, safe condition, the electrical equipment and facilities must be maintained properly.
Dust and dirt, damaged enclosures and components, corrosion, loose connections, and reduced operating clearances can be the cause of employee injuries.
Some of these conditions can also lead to fire. A thorough, periodic preventive maintenance plan should be established as soon as new facilities and equipment are installed.
Local procedures should be created as soon as possible to cover the maintenance of electrical equipment. Most of this information can be obtained from recognized standards and manufacturer's literature.
Proper operation and maintenance are important to electrical safety because when things do not function as designed or planned, the results may be unexpected.
Many injuries and fatalities have occurred when the unexpected happened. NFPA 70B-1998 is an excellent guide to recommended practices for maintenance of electrical equipment.
It also contains the "why's" and the "wherefore's" of an electrical maintenance program, as well as guidance for maintaining and testing specific types of electrical equipment.
In addition, it contains information in its appendix regarding the suggested frequencies for performance of maintenance and testing. This is a good document to review while facilities are being installed.
Dust and dirt, damaged enclosures and components, corrosion, loose connections, and reduced operating clearances can be the cause of employee injuries.
Some of these conditions can also lead to fire. A thorough, periodic preventive maintenance plan should be established as soon as new facilities and equipment are installed.
Local procedures should be created as soon as possible to cover the maintenance of electrical equipment. Most of this information can be obtained from recognized standards and manufacturer's literature.
Proper operation and maintenance are important to electrical safety because when things do not function as designed or planned, the results may be unexpected.
Many injuries and fatalities have occurred when the unexpected happened. NFPA 70B-1998 is an excellent guide to recommended practices for maintenance of electrical equipment.
It also contains the "why's" and the "wherefore's" of an electrical maintenance program, as well as guidance for maintaining and testing specific types of electrical equipment.
In addition, it contains information in its appendix regarding the suggested frequencies for performance of maintenance and testing. This is a good document to review while facilities are being installed.
SOLID GROUNDING OF POWER SYSTEM BASIC INFORMATION AND TUTORIALS
What is a solidly grounded system?
Solid grounding refers to the connection of the neutral of a generator, power transformer, or grounding transformer directly to the station ground or to the earth. Because of the reactance of the grounded generator or transformer in series with the neutral circuit, a solid ground connection does not provide a zero-impedance neutral circuit.
If the reactance of the system zero-sequence circuit is too great with respect to the system positive-sequence reactance, the objectives sought in grounding, principally freedom from transient overvoltages, may not be achieved.
This is rarely a problem in typical industrial and commercial power systems. The zero-sequence impedance of most generators used in these systems is much lower than the positive-sequence impedance of these generators.
The zero-sequence impedance of a delta-wye transformer will not exceed the transformer's positive sequence impedance. There are, however, conditions under which relatively high zero-sequence impedance may occur.
One of these conditions is a power system fed by several generators and/or transformers in parallel. If the neutral of only one source is grounded, it is possible for the zero-sequence impedance of the grounded source to exceed the effective positive-sequence impedance of the several sources in parallel.
Another such condition may occur where power is distributed to remote facilities by an overhead line without a metallic ground return path. In this case, the return path for ground-fault current is through the earth, and, even though both the neutral of the source and the nonconducting parts at the load may be grounded with well-made electrodes, the ground return path includes the impedance of both of these ground electrodes.
This impedance may be significant. Another significant source of zero sequence impedance is the large line-to-ground spacing of the overhead line.
To ensure the benefits of solid grounding, it is necessary to determine the degree of grounding provided in the system. A good guide in answering this question is the magnitude of ground-fault current as compared to the system threephase fault current.
The higher the ground-fault current in relation to the three-phase fault current the greater the degree of grounding in the system.
Effectively grounded systems will have a line-to-ground short circuit current of at least 60% of the three-phase short-circuit value. In terms of resistance and reactance, effective grounding of a system is accomplished only when R0</=X1 and X0 </= 3X1 and such relationships exist at any point in the system.
The X1 component used in the above relation is the Thevenin equivalent positive-sequence reactance of the complete system including the subtransient reactance of all rotating machines.
Application of surge arresters for grounded-neutral service requires that the system be effectively grounded.
REACTANCE GROUNDING OF POWER SYSTEM BASIC INFORMATION
What is reactance grounding? How reactance grounding is beneficial?
The term reactance grounding describes the case in which a reactor is connected between the system neutral and ground.
Since the ground-fault that may flow in a reactance-grounded system is a function of the neutral reactance, the magnitude of the ground-fault current is often used as a criterion for describing the degree of grounding.
In a reactance-grounded system, the available ground-fault current should be at least 25% and preferably 60% of the threephase fault current to prevent serious transient overvoltages (X0 </=X1).
This is considerably higher than the level of fault current desirable in a resistance-grounded system, and therefore reactance grounding is usually not considered an alternative to resistance grounding.
In most generators, solid grounding, that is, grounding without external impedance, may permit the maximum ground fault current from the generator to exceed the maximum three-phase fault current that the generator can deliver and for which its windings are braced.
Consequently, neutral-grounded generators should be grounded through a low-value reactor that will limit the ground-fault current to a value no greater than the generator three-phase fault current.
In the case of three-phase four-wire systems, the limitation of ground-fault current to 100% of the three-phase fault current is usually practical without interfering with normal four-wire operation.
In practice, reactance grounding is generally used only in this case and to ground substation transformers with similar characteristics.
The term reactance grounding describes the case in which a reactor is connected between the system neutral and ground.
Since the ground-fault that may flow in a reactance-grounded system is a function of the neutral reactance, the magnitude of the ground-fault current is often used as a criterion for describing the degree of grounding.
In a reactance-grounded system, the available ground-fault current should be at least 25% and preferably 60% of the threephase fault current to prevent serious transient overvoltages (X0 </=X1).
This is considerably higher than the level of fault current desirable in a resistance-grounded system, and therefore reactance grounding is usually not considered an alternative to resistance grounding.
In most generators, solid grounding, that is, grounding without external impedance, may permit the maximum ground fault current from the generator to exceed the maximum three-phase fault current that the generator can deliver and for which its windings are braced.
Consequently, neutral-grounded generators should be grounded through a low-value reactor that will limit the ground-fault current to a value no greater than the generator three-phase fault current.
In the case of three-phase four-wire systems, the limitation of ground-fault current to 100% of the three-phase fault current is usually practical without interfering with normal four-wire operation.
In practice, reactance grounding is generally used only in this case and to ground substation transformers with similar characteristics.
BURNS FROM ELECTRICAL ARCS OT ARC FLASH BASIC INFORMATION
Almost everyone is aware that electrical shock can be a hazard to life. Many people, however, have experienced minor shocks with no dire consequences. This tends to make people somewhat complacent around electricity.
What most people don't know is that approximately half of the serious electrical injuries involve burns. Electrical burns include not only burns from contact, but also radiation burns from the fierce fire of electric arcs that result from short circuits due to poor electrical contact or insulation failure.
The electric arc between metals is, next to the laser, the hottest thing on earth. It is about four times as hot as the sun's surface.
Where high arc currents are involved, burns from such arcs can be fatal, even when the victim is some distance from the arc. Serious or fatal burns can occur at distances of more than 304 cm (10 ft) from the source of a flash.
In addition to burns from the flash itself, clothing is often ignited. Fatal burns can result because the clothing cannot be removed or extinguished quickly enough to prevent serious burns over much of the body.
Thus, even at what a person thinks to be a large distance, serious or fatal injuries can occur to a person's bare skin or skin covered with flammable clothing as a result of a severe power arc. Electrical workers are frequently in the vicinity of energized parts.
It is only the relative infrequency of such arcs that has limited the number of injuries. Examples of exposure are working on open panelboards or switchboards, hook stick operation of medium-voltage fuses, testing of cable terminals, grounding before testing, or working in manholes near still-energized cables.
Several studies, tests, and technical papers are being written on the subject of the flash hazard. Safety standards and procedures are being developed to recognize the fact that arcs can cause serious injuries at significant distances from energized sources.
Equally important in these new safety standards is the fact that, in many cases, only trained people with arc protective equipment should approach exposed energized electrical equipment. Spectators should stay away because, even though they think they are far enough away, they generally don't have an understanding of what is a safe approach distance.
Depending upon the fault energy available, spectators can be seriously hurt at large distances from the point of an arc.
What most people don't know is that approximately half of the serious electrical injuries involve burns. Electrical burns include not only burns from contact, but also radiation burns from the fierce fire of electric arcs that result from short circuits due to poor electrical contact or insulation failure.
The electric arc between metals is, next to the laser, the hottest thing on earth. It is about four times as hot as the sun's surface.
Where high arc currents are involved, burns from such arcs can be fatal, even when the victim is some distance from the arc. Serious or fatal burns can occur at distances of more than 304 cm (10 ft) from the source of a flash.
In addition to burns from the flash itself, clothing is often ignited. Fatal burns can result because the clothing cannot be removed or extinguished quickly enough to prevent serious burns over much of the body.
Thus, even at what a person thinks to be a large distance, serious or fatal injuries can occur to a person's bare skin or skin covered with flammable clothing as a result of a severe power arc. Electrical workers are frequently in the vicinity of energized parts.
It is only the relative infrequency of such arcs that has limited the number of injuries. Examples of exposure are working on open panelboards or switchboards, hook stick operation of medium-voltage fuses, testing of cable terminals, grounding before testing, or working in manholes near still-energized cables.
Several studies, tests, and technical papers are being written on the subject of the flash hazard. Safety standards and procedures are being developed to recognize the fact that arcs can cause serious injuries at significant distances from energized sources.
Equally important in these new safety standards is the fact that, in many cases, only trained people with arc protective equipment should approach exposed energized electrical equipment. Spectators should stay away because, even though they think they are far enough away, they generally don't have an understanding of what is a safe approach distance.
Depending upon the fault energy available, spectators can be seriously hurt at large distances from the point of an arc.
NATURE OF ELECTRICAL ARCS BASIC INFORMATION AND TUTORIALS
What are arcing? What is the effect of electrical arcing?
Electrical arcing is the term that is applied to the passage of substantial electrical currents through what had previously been air. It is initiated by flashover or the introduction of some conductive material.
Current passage is through ionized air and the vapor of the arc terminal material, which is usually a conductive metal or carbon. In contrast to current flow through low-pressure gases such as neon, arcing involves high temperatures of up to, or beyond, 20 000 °K (35 000 °F) at the arc terminals.
No materials on earth can withstand these temperatures; all materials are not only melted, but vaporized. Actually, 20 000 °K (35 000 °F) is about four times as hot as the surface temperature of the sun.
The vapor of the terminal material has substantially higher resistance than solid metal, to the extent that the voltage drop in the arc ranges from 29.53 V/cm (75 V/in) to 39.37 V/cm (100 V/in), which is several thousand times the voltage drop in a solid conductor.
Since the inductance of the arc path is not appreciably different from that of a solid conductor of the same length, the arc current path is substantially resistive in nature, thus yielding unity power factor. Voltage drop in a faulted large solid or stranded conductor is about 0.016-0.033 V/cm (0.5-1 V/ft).
For low-voltage circuits, an arc length of 29.53-39.37 V/cm (75-100 V/in) consumes a substantial portion of the available voltage, leaving only the difference between source voltage and arc voltage to force the fault current through the total system impedance, including that of the arc. This is the reason for the "stabilization" of arc current on 480 Y/277 V circuits when the arc length is of the order of 10.16 cm (4 in), such as with bus spacing.
For higher voltages, the arc lengths can be substantially greater, e.g., 2.54 cm (1 in) per 100 V of supply, before the system impedance starts to regulate or limit the fault current. Note that the arc voltage drop and the source voltage drop add in quadrature, the former resistive, the latter substantially reactive.
The length or size of arcs in the higher voltage systems thus can be greater and can readily bridge the gap from energized parts to ground or other polarities with little drop in fault current.
The hazard of the arc is not only due to the level of voltage. Under some cases it is possible to generate a higher energy arc from a lower voltage than from a higher voltage.
The amount of arc energy generated is dependent upon the amount of short-circuit current available and the amount of time before the fault causing the arc is cleared (removed from the power source) by a circuit breaker or fuse.
Electrical arcing is the term that is applied to the passage of substantial electrical currents through what had previously been air. It is initiated by flashover or the introduction of some conductive material.
Current passage is through ionized air and the vapor of the arc terminal material, which is usually a conductive metal or carbon. In contrast to current flow through low-pressure gases such as neon, arcing involves high temperatures of up to, or beyond, 20 000 °K (35 000 °F) at the arc terminals.
No materials on earth can withstand these temperatures; all materials are not only melted, but vaporized. Actually, 20 000 °K (35 000 °F) is about four times as hot as the surface temperature of the sun.
The vapor of the terminal material has substantially higher resistance than solid metal, to the extent that the voltage drop in the arc ranges from 29.53 V/cm (75 V/in) to 39.37 V/cm (100 V/in), which is several thousand times the voltage drop in a solid conductor.
Since the inductance of the arc path is not appreciably different from that of a solid conductor of the same length, the arc current path is substantially resistive in nature, thus yielding unity power factor. Voltage drop in a faulted large solid or stranded conductor is about 0.016-0.033 V/cm (0.5-1 V/ft).
For low-voltage circuits, an arc length of 29.53-39.37 V/cm (75-100 V/in) consumes a substantial portion of the available voltage, leaving only the difference between source voltage and arc voltage to force the fault current through the total system impedance, including that of the arc. This is the reason for the "stabilization" of arc current on 480 Y/277 V circuits when the arc length is of the order of 10.16 cm (4 in), such as with bus spacing.
For higher voltages, the arc lengths can be substantially greater, e.g., 2.54 cm (1 in) per 100 V of supply, before the system impedance starts to regulate or limit the fault current. Note that the arc voltage drop and the source voltage drop add in quadrature, the former resistive, the latter substantially reactive.
The length or size of arcs in the higher voltage systems thus can be greater and can readily bridge the gap from energized parts to ground or other polarities with little drop in fault current.
The hazard of the arc is not only due to the level of voltage. Under some cases it is possible to generate a higher energy arc from a lower voltage than from a higher voltage.
The amount of arc energy generated is dependent upon the amount of short-circuit current available and the amount of time before the fault causing the arc is cleared (removed from the power source) by a circuit breaker or fuse.
OIL TESTING OF POWER EQUIPMENT BASIC INFORMATION AND TUTORIALS
Why do we conduct oil testing of our power equipment?
Many medium- and high-voltage transformers and circuit breakers utilize different types of oils for insulation. Chemical testing of the oil has proven to be a very dependable method of locating existing or potential problems.
Only a brief overview of some of the common tests can be provided here.
One of the most obvious problems that would significantly reduce the insulation value of the oil is contamination such as moisture or, for circuit breakers and load top changers, carbon.
This can be tested on-site by measuring the voltage at which dielectric breakdown occurs with a special test set that is designed for this purpose.
Oil samples may be sent to a testing laboratory for a series of tests. Measurements of the acidity give an indication of how much oxidation or contamination the oil has experienced.
Interfacial tension, the force that is required to rupture the surface tension at an oil-water interface, is also an indication of possible oxidation or contamination.
One of the most successful tests in determining if a transformer winding has experienced hot spots, corona discharge, or arcing is the dissolved gas analysis test. An oil sample is taken with a special cylinder that is air tight, and the gases that are dissolved in the oil are analyzed.
By determining the type and amount of gas that has been dissolved in the oil, predictions can be made about the internal integrity of the transformer winding.
Many medium- and high-voltage transformers and circuit breakers utilize different types of oils for insulation. Chemical testing of the oil has proven to be a very dependable method of locating existing or potential problems.
Only a brief overview of some of the common tests can be provided here.
One of the most obvious problems that would significantly reduce the insulation value of the oil is contamination such as moisture or, for circuit breakers and load top changers, carbon.
This can be tested on-site by measuring the voltage at which dielectric breakdown occurs with a special test set that is designed for this purpose.
Oil samples may be sent to a testing laboratory for a series of tests. Measurements of the acidity give an indication of how much oxidation or contamination the oil has experienced.
Interfacial tension, the force that is required to rupture the surface tension at an oil-water interface, is also an indication of possible oxidation or contamination.
One of the most successful tests in determining if a transformer winding has experienced hot spots, corona discharge, or arcing is the dissolved gas analysis test. An oil sample is taken with a special cylinder that is air tight, and the gases that are dissolved in the oil are analyzed.
By determining the type and amount of gas that has been dissolved in the oil, predictions can be made about the internal integrity of the transformer winding.
INFRARED SCANNING FOR HOTSPOT OF ELECTRICAL COMPONENTS BASIC INFORMATION
What is Infrared Scanning? How is it done?
Infrared scanning is a method that is utilized to locate high-resistance connections ("hot spots") by using a camera that turns infrared radiation into a visible image.
This test is performed with the equipment in service carrying normal load current, which is a major advantage because it does not interrupt normal production. Exposure to energized equipment, of course, carries the possibility of exposure to electrical hazards.
The operator shall recognize and deal with such potential hazards accordingly.
The most common use of infrared scanning is to locate loose or corroded connections in switchboards, panel boards, bus ways, and motor starters.
It is a comparative type test in which the person who performs the scan is looking for an area that appears brighter (hotter) than a similar area, such as a lug connection on phase "A" as it compares to similar connections on phases "B" and "C"
The person should be aware of how unbalanced loading may affect heating, thereby giving an indication similar to looseness.
One limitation of infrared scanning is that the equipment has to be carrying enough load for the hot spots to be visible.
At lower loads, there may not be enough heat generated to locate a problem, even when the connections are significantly looser than they should be.
Infrared scanning is a method that is utilized to locate high-resistance connections ("hot spots") by using a camera that turns infrared radiation into a visible image.
This test is performed with the equipment in service carrying normal load current, which is a major advantage because it does not interrupt normal production. Exposure to energized equipment, of course, carries the possibility of exposure to electrical hazards.
The operator shall recognize and deal with such potential hazards accordingly.
The most common use of infrared scanning is to locate loose or corroded connections in switchboards, panel boards, bus ways, and motor starters.
It is a comparative type test in which the person who performs the scan is looking for an area that appears brighter (hotter) than a similar area, such as a lug connection on phase "A" as it compares to similar connections on phases "B" and "C"
The person should be aware of how unbalanced loading may affect heating, thereby giving an indication similar to looseness.
One limitation of infrared scanning is that the equipment has to be carrying enough load for the hot spots to be visible.
At lower loads, there may not be enough heat generated to locate a problem, even when the connections are significantly looser than they should be.
MOTOR SURGE COMPARISON TESTING BASIC INFORMATION AND TUTORIALS
What is Motor surge comparison testing? How is it done?
Motor surge comparison testing addresses the problem of insufficient test voltage to find the weak insulation between turns by utilizing a high-voltage pulse. Two identical high-voltage pulses are introduced into two windings of a motor.
The propagation of the pulse through one winding is compared to the propagation of the identical pulse through the winding next to it.
An oscilloscope (usually built into the surge tester) is used to look at the traces and to compare them. The patterns should be identical (or very nearly so) and can appear as one trace (two superimposed traces) if both windings are good.
A turn-to-turn failure (or a failure to ground) is indicated by two distinctly different traces appearing on the oscilloscope.
Motor surge comparison testing has been used by motor winding shops for many years. There are now portable models that are available for field testing.
Motor surge comparison testing has proven to be a valuable tool in detecting the early stages of a winding failure, both from the standpoint of preventing an unexpected failure during operation and preventing a catastrophic failure of the motor so it can be repaired instead of needing to be replaced.
Motor surge comparison testing addresses the problem of insufficient test voltage to find the weak insulation between turns by utilizing a high-voltage pulse. Two identical high-voltage pulses are introduced into two windings of a motor.
The propagation of the pulse through one winding is compared to the propagation of the identical pulse through the winding next to it.
An oscilloscope (usually built into the surge tester) is used to look at the traces and to compare them. The patterns should be identical (or very nearly so) and can appear as one trace (two superimposed traces) if both windings are good.
A turn-to-turn failure (or a failure to ground) is indicated by two distinctly different traces appearing on the oscilloscope.
Motor surge comparison testing has been used by motor winding shops for many years. There are now portable models that are available for field testing.
Motor surge comparison testing has proven to be a valuable tool in detecting the early stages of a winding failure, both from the standpoint of preventing an unexpected failure during operation and preventing a catastrophic failure of the motor so it can be repaired instead of needing to be replaced.
TRANSFORMER TURNS RATIO TESTING BASIC INFORMATION AND TUTORIALS
What is Transformer turns ratio (TTR) testing? How is it done?
The voltage across the primary of a transformer is directly proportional to the voltage across the secondary, multiplied by the ratio of primary winding turns to secondary winding turns.
In order to ensure that the transformer was wound properly when it was new, and to help locate subsequent turn-to-turn faults in the winding, it is common practice to perform a TTR test.
The simplest method would be to energize one primary winding with a known voltage (that is less than or equal to the windingÕs rating) and measure the voltage on the other winding.
Since source test voltages can fluctuate, it is often more accurate to use a test set, designed for this purpose, that creates the test voltage internally, thus giving a direct read-out of the ratio measured.
The voltage across the primary of a transformer is directly proportional to the voltage across the secondary, multiplied by the ratio of primary winding turns to secondary winding turns.
In order to ensure that the transformer was wound properly when it was new, and to help locate subsequent turn-to-turn faults in the winding, it is common practice to perform a TTR test.
The simplest method would be to energize one primary winding with a known voltage (that is less than or equal to the windingÕs rating) and measure the voltage on the other winding.
Since source test voltages can fluctuate, it is often more accurate to use a test set, designed for this purpose, that creates the test voltage internally, thus giving a direct read-out of the ratio measured.
WINDING AND CONTACT RESISTANCE TEST BASIC INFORMATION AND TUTORIALS
What are winding and contact resistance testing?
Winding and contact resistance are similar in that both are looking for a very low ohmic value, since they are measuring the "resistance" of a component that is supposed to conduct electricity.
A Kelvin Bridge has long been a standard method of measuring low values of resistance, and is still in use today.
With the advent of electronics, there are digital meters available that also are capable of measuring very low values (milliohms or microohms) of resistance.
The typical low-resistance ohmmeter uses four terminals (to eliminate lead resistance) in which a dc current is injected into the conductor to be measured and the voltage drop across the conductor is measured.
Contact resistance test sets can be used to measure the resistance of bus joints and cable joints, as well as the closed contacts of a circuit breaker or motor starter.
In many cases, it is a comparative type test in which the resistance of one set of contacts is compared to the readings obtained from the other two phases of the same, or a similar, piece of equipment.
Winding resistance differs from contact resistance in that the inductance of large windings can interfere with the operation of the test set.
There are test sets, available commercially, that are designed specifically for large transformer and motor windings, for cases in which a standard low-resistance ohmmeter is not adequate.
Winding and contact resistance are similar in that both are looking for a very low ohmic value, since they are measuring the "resistance" of a component that is supposed to conduct electricity.
A Kelvin Bridge has long been a standard method of measuring low values of resistance, and is still in use today.
With the advent of electronics, there are digital meters available that also are capable of measuring very low values (milliohms or microohms) of resistance.
The typical low-resistance ohmmeter uses four terminals (to eliminate lead resistance) in which a dc current is injected into the conductor to be measured and the voltage drop across the conductor is measured.
Contact resistance test sets can be used to measure the resistance of bus joints and cable joints, as well as the closed contacts of a circuit breaker or motor starter.
In many cases, it is a comparative type test in which the resistance of one set of contacts is compared to the readings obtained from the other two phases of the same, or a similar, piece of equipment.
Winding resistance differs from contact resistance in that the inductance of large windings can interfere with the operation of the test set.
There are test sets, available commercially, that are designed specifically for large transformer and motor windings, for cases in which a standard low-resistance ohmmeter is not adequate.
PREVENTIVE MAINTENANCE DESIGN CONSIDERATIONS BASIC INFORMATION
The best preventive maintenance programs start during the design of the facility. A key design consideration in order to support preventive maintenance is to accommodate planned power outages so that maintenance activities can proceed.
For example, if delivery of power is not a 24 hour necessity, then extended outages after normal work hours can be allowed for maintenance activities. Otherwise, consider design features that can speed up the maintenance process or reduce the duration of the outage to loads.
These might include redundant circuits, alternate power sources, or protective devices such as drawout circuit breakers (rather than fixed-mount circuit breakers).
Additional consideration should be given to the accessibility of the electrical equipment for maintenance. Circuit breaker location can be critical to the maintenance process.
An example would be circuit breakers that are installed in a basement that has only stairway access through which equipment can be brought down to the circuit breaker location. In addition, access to the back of switchboards or switchgear, as opposed to their being mounted against the wall, may be necessary in order to perform thorough maintenance.
The environment in which the equipment is installed can play an important part in maintenance. Where equipment is mounted (inside or outside) and whether it is properly enclosed and protected from dust, moisture, and chemical contamination are all factors that influence the frequency with which maintenance tasks should be performed.
The design phase is also the period in which the establishment of baseline data for the equipment should be considered. This can be done by including in the design specifications the acceptance or start-up testing of the equipment when it is Þrst installed. The InterNational Electrical Testing Association (NETA) provides detailed specifications for electrical power equipment in NETA ATS-1995 [B1].
Design drawings are very important to an effective maintenance program. As-built drawings should be kept up-to-date. An accurate single-line diagram is crucial to the effective and safe operation of the equipment.
This helps the operator to understand the consequences of switching a circuit that can interrupt power in an undesirable or unplanned mode. More significantly, it can help avoid the accidental energization of equipment.
As part of the procurement of the electrical equipment, consideration should be given to the tools and instruments that are required to perform effective maintenance, such as hoists or manual-lift trucks that are used to remove and install circuit breakers. These tools and instruments will help to ensure safety and productivity. Finally, the installation, operation, and maintenance manuals should be obtained and filed.
For example, if delivery of power is not a 24 hour necessity, then extended outages after normal work hours can be allowed for maintenance activities. Otherwise, consider design features that can speed up the maintenance process or reduce the duration of the outage to loads.
These might include redundant circuits, alternate power sources, or protective devices such as drawout circuit breakers (rather than fixed-mount circuit breakers).
Additional consideration should be given to the accessibility of the electrical equipment for maintenance. Circuit breaker location can be critical to the maintenance process.
An example would be circuit breakers that are installed in a basement that has only stairway access through which equipment can be brought down to the circuit breaker location. In addition, access to the back of switchboards or switchgear, as opposed to their being mounted against the wall, may be necessary in order to perform thorough maintenance.
The environment in which the equipment is installed can play an important part in maintenance. Where equipment is mounted (inside or outside) and whether it is properly enclosed and protected from dust, moisture, and chemical contamination are all factors that influence the frequency with which maintenance tasks should be performed.
The design phase is also the period in which the establishment of baseline data for the equipment should be considered. This can be done by including in the design specifications the acceptance or start-up testing of the equipment when it is Þrst installed. The InterNational Electrical Testing Association (NETA) provides detailed specifications for electrical power equipment in NETA ATS-1995 [B1].
Design drawings are very important to an effective maintenance program. As-built drawings should be kept up-to-date. An accurate single-line diagram is crucial to the effective and safe operation of the equipment.
This helps the operator to understand the consequences of switching a circuit that can interrupt power in an undesirable or unplanned mode. More significantly, it can help avoid the accidental energization of equipment.
As part of the procurement of the electrical equipment, consideration should be given to the tools and instruments that are required to perform effective maintenance, such as hoists or manual-lift trucks that are used to remove and install circuit breakers. These tools and instruments will help to ensure safety and productivity. Finally, the installation, operation, and maintenance manuals should be obtained and filed.
PREVENTIVE MAINTENANCE PHILOSOPHY BASIC INFORMATION
What are the philosophies of preventive maintenance?
Most people recognize the need for the maintenance of electrical equipment. The debate really focuses on how much maintenance is enough.
The key to the discussion over the proper amount of maintenance centers on the economic balance between the cost of performing maintenance and the importance of reliable power.
For example, a computer center with a downtime cost of $100 000 or more an hour would justify a much more extensive maintenance program than would a small facility whose downtime cost might be minuscule in comparison.
Moreover, it has been shown that there is a balance to the amount of economic benefit that is achieved from performing maintenance. A lack of maintenance eventually results in failures and a high cost to a plant.
Likewise, an extreme amount of maintenance is wasteful and also results in a high cost to a plant. The optimum maintenance program lies somewhere in between.
This balance point can vary for different types of facilities. There are two benefits to having an effective preventive maintenance program. The first is that costs are reduced through the minimizing of equipment downtime.
The second benefit is obtained through improved safety and system performance. Other intangible benefits include things such as improved employee morale, better workmanship, increased productivity, reduced absenteeism, reduced interruption of production, and improved insurance considerations.
In planning an electrical preventive maintenance (EPM) program, consideration must be given to the costs of safety, the costs associated with direct losses due to equipment damage, and the indirect costs associated with downtime or lost or inefficient production.
Most people recognize the need for the maintenance of electrical equipment. The debate really focuses on how much maintenance is enough.
The key to the discussion over the proper amount of maintenance centers on the economic balance between the cost of performing maintenance and the importance of reliable power.
For example, a computer center with a downtime cost of $100 000 or more an hour would justify a much more extensive maintenance program than would a small facility whose downtime cost might be minuscule in comparison.
Moreover, it has been shown that there is a balance to the amount of economic benefit that is achieved from performing maintenance. A lack of maintenance eventually results in failures and a high cost to a plant.
Likewise, an extreme amount of maintenance is wasteful and also results in a high cost to a plant. The optimum maintenance program lies somewhere in between.
This balance point can vary for different types of facilities. There are two benefits to having an effective preventive maintenance program. The first is that costs are reduced through the minimizing of equipment downtime.
The second benefit is obtained through improved safety and system performance. Other intangible benefits include things such as improved employee morale, better workmanship, increased productivity, reduced absenteeism, reduced interruption of production, and improved insurance considerations.
In planning an electrical preventive maintenance (EPM) program, consideration must be given to the costs of safety, the costs associated with direct losses due to equipment damage, and the indirect costs associated with downtime or lost or inefficient production.
POWER SYSTEM FAULT CLEARING PROCEDURE BASIC INFORMATION
The complexity of the system normally determines the level of detail planning that is required for system clearing procedures. A simple, single-source, radial supply system may only require opening a single switch or circuit breaker for circuit isolation.
The clearing procedures for even so simple a case, however, should include checking to ensure that no other sources exist and that the correct isolating device is being operated. It is important that all persons who may be exposed to a hazard, as a result of a switching action, be notified prior to the action.
Complex power distribution systems that require several switching steps to isolate a portion of the system require more elaborate clearing procedures. It is necessary to use written switching instructions for systems that may have several sources into an area.
When written instructions are used, a third party, who is familiar with the power system, should review them for errors and omissions. The consequences of learning about switching errors while in the act of switching are usually costly, especially when the wrong portion of the system is accidentally de-energized. It is important that written procedures be shared with all persons who are involved in the switching process.
A single-line diagram should accompany the written switching instructions so that the switch operator can keep track of the progress through the system. A real-time, single-line mimic bus on a very complex system allows for the independent monitoring of the switching process through the system as component status is changed.
Some mimic-bus systems allow the operator to simulate switching of the system off-line, which allows for the detection of possible errors before the actual switching is performed.
The clearing procedures should be completely written, checked, and understood by all persons involved before they are applied to any portion of the power distribution system. The instructions and/or procedures should include a verification that the power has been removed (by live-line testing or other means) followed by the placement of grounds and the locking/ tagging of isolating devices.
The clearing procedures for even so simple a case, however, should include checking to ensure that no other sources exist and that the correct isolating device is being operated. It is important that all persons who may be exposed to a hazard, as a result of a switching action, be notified prior to the action.
Complex power distribution systems that require several switching steps to isolate a portion of the system require more elaborate clearing procedures. It is necessary to use written switching instructions for systems that may have several sources into an area.
When written instructions are used, a third party, who is familiar with the power system, should review them for errors and omissions. The consequences of learning about switching errors while in the act of switching are usually costly, especially when the wrong portion of the system is accidentally de-energized. It is important that written procedures be shared with all persons who are involved in the switching process.
A single-line diagram should accompany the written switching instructions so that the switch operator can keep track of the progress through the system. A real-time, single-line mimic bus on a very complex system allows for the independent monitoring of the switching process through the system as component status is changed.
Some mimic-bus systems allow the operator to simulate switching of the system off-line, which allows for the detection of possible errors before the actual switching is performed.
The clearing procedures should be completely written, checked, and understood by all persons involved before they are applied to any portion of the power distribution system. The instructions and/or procedures should include a verification that the power has been removed (by live-line testing or other means) followed by the placement of grounds and the locking/ tagging of isolating devices.
ELECTRICAL SAFE PRACTICES PROCEDURE OUTLINE BASIC INFORMATION
Typical outline of an electrical safe practices procedure
-Title. The title identifies the specific equipment where the procedure applies.
-Purpose. The purpose is to identify the task to be performed.
-Qualification. The training and knowledge that qualified personnel shall possess in order to perform particular tasks are identified.
-Hazard identification. The hazards that were identified during development of the procedure are highlighted. These are the hazards that may not appear obvious to personnel performing work on or near the energized equipment.
-Hazard classification. The degree of risk, as deÞned by the hazard/risk analysis, is identified for the particular task to be performed.
-Limits of approach. The approach distances and restrictions are identified for personnel access around energized electrical equipment.
-Safe work practices. The controls that shall be in place prior to, and during the performance of, work on or near energized equipment are emphasized.
-Personnel protective clothing and equipment. The minimum types and amounts of protective clothing and equipment that are required by personnel to perform the tasks described in the procedures are listed. Personnel performing the work shall wear the protective clothing at all times while performing the tasks identified in the procedure.
-Test equipment and tools. All the test equipment and tools that are required to perform the work described in this procedure are listed. The test equipment and tools shall be maintained and operated in accordance with the manufacturer's instructions.
-Reference data. The reference material used in the development of the procedure is listed. It includes the appropriate electrical single-line diagrams, equipment rating (voltage level), and manufacturer's operating instructions.
-Procedure steps. The steps required by qualified personnel wearing personal protective clothing and using the approved test equipment to perform specific tasks in a specified manner are identified.
-Sketches. Sketches are used, where necessary, to properly illustrate and elaborate specific tasks.
-Title. The title identifies the specific equipment where the procedure applies.
-Purpose. The purpose is to identify the task to be performed.
-Qualification. The training and knowledge that qualified personnel shall possess in order to perform particular tasks are identified.
-Hazard identification. The hazards that were identified during development of the procedure are highlighted. These are the hazards that may not appear obvious to personnel performing work on or near the energized equipment.
-Hazard classification. The degree of risk, as deÞned by the hazard/risk analysis, is identified for the particular task to be performed.
-Limits of approach. The approach distances and restrictions are identified for personnel access around energized electrical equipment.
-Safe work practices. The controls that shall be in place prior to, and during the performance of, work on or near energized equipment are emphasized.
-Personnel protective clothing and equipment. The minimum types and amounts of protective clothing and equipment that are required by personnel to perform the tasks described in the procedures are listed. Personnel performing the work shall wear the protective clothing at all times while performing the tasks identified in the procedure.
-Test equipment and tools. All the test equipment and tools that are required to perform the work described in this procedure are listed. The test equipment and tools shall be maintained and operated in accordance with the manufacturer's instructions.
-Reference data. The reference material used in the development of the procedure is listed. It includes the appropriate electrical single-line diagrams, equipment rating (voltage level), and manufacturer's operating instructions.
-Procedure steps. The steps required by qualified personnel wearing personal protective clothing and using the approved test equipment to perform specific tasks in a specified manner are identified.
-Sketches. Sketches are used, where necessary, to properly illustrate and elaborate specific tasks.
WORK AUTHORIZATION - WORK PERMITS FOR ELECTRICAL WORKS
Before beginning any work, particularly in an existing operating facility, a person should receive a request to do the work from the custodian, thoroughly plan the job, review the job plan with the custodian, and obtain permission from the facility manager to proceed with the work.
Some kind of work authorization document is advisable to ensure that everyone who may be affected is aware of what is going on. In addition to approvals, this document could contain a checklist of safety items that should be considered before proceeding with the work.
The work authorization document forces people to think about the safety aspects of the job. This concept applies to all kinds of work, not just electrical.
Again, when performing electrical work in a country other than the U.S., make sure that any laws of the country that may be applicable to the job being performed are known.
Some kind of work authorization document is advisable to ensure that everyone who may be affected is aware of what is going on. In addition to approvals, this document could contain a checklist of safety items that should be considered before proceeding with the work.
The work authorization document forces people to think about the safety aspects of the job. This concept applies to all kinds of work, not just electrical.
Again, when performing electrical work in a country other than the U.S., make sure that any laws of the country that may be applicable to the job being performed are known.
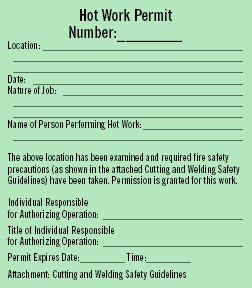
INSTRUMENT TRANSFORMERS TESTING BASIC INFORMATION AND TUTORIALS
What is instrument transformer testing?
There are two common designations of instrument transformers: CTs and voltage transformers (VTs) or potential transformers (PTs). The function of an instrument transformer is to reduce the level of voltage or current so that the protective relay (or metering) does not have to be rated for full line voltage or current.
The insulation resistance, transformer ratio, and polarity may be tested in both CTs and VTs. The ratio is the number of turns of wire in the primary winding divided by the number of turns of wire in the secondary winding.
The polarity is determined by which way the wire was wrapped around the iron core. This determines the relationship between the primary winding terminal (H1) and the secondary winding terminal (X1) so that X1 is positive with respect to X2 at the same time that H1 is positive with respect to H2.
The correctness of polarity is important to the correct operation of many relays and metering instruments. CTs often have two additional tests performed: "burden" and "saturation" tests. The burden on a CT is the amount of impedance connected to the secondary winding as a load, usually in the form of protective relays or metering.
The burden test consists of injecting a known current level (usually 1-5 A ac) into the load (usually from the shorting terminal block of the CT) and measuring the voltage at the point of injection. The impedance (or burden) of the circuit is the ratio of the voltage measured to the current injected.
A saturation test is performed to find out the voltage at which the iron in the CT saturates. A known voltage source is connected to the secondary of the transformer and is raised in steps, while the current value is recorded at each step.
When saturation is reached, the given voltage changes cause much smaller changes in current. The saturation test is used in conjunction with the burden test to make sure that the CT is capable of operating the load (usually protective relays) to which it may be subjected.
If the burden on the CT is too high, it may go into saturation and be unable to maintain its proper ratio. When this happens, protective relays may trip too slowly or not at all due to an insufficient level of current from the CT secondary.
There are two common designations of instrument transformers: CTs and voltage transformers (VTs) or potential transformers (PTs). The function of an instrument transformer is to reduce the level of voltage or current so that the protective relay (or metering) does not have to be rated for full line voltage or current.
The insulation resistance, transformer ratio, and polarity may be tested in both CTs and VTs. The ratio is the number of turns of wire in the primary winding divided by the number of turns of wire in the secondary winding.
The polarity is determined by which way the wire was wrapped around the iron core. This determines the relationship between the primary winding terminal (H1) and the secondary winding terminal (X1) so that X1 is positive with respect to X2 at the same time that H1 is positive with respect to H2.
The correctness of polarity is important to the correct operation of many relays and metering instruments. CTs often have two additional tests performed: "burden" and "saturation" tests. The burden on a CT is the amount of impedance connected to the secondary winding as a load, usually in the form of protective relays or metering.
The burden test consists of injecting a known current level (usually 1-5 A ac) into the load (usually from the shorting terminal block of the CT) and measuring the voltage at the point of injection. The impedance (or burden) of the circuit is the ratio of the voltage measured to the current injected.
A saturation test is performed to find out the voltage at which the iron in the CT saturates. A known voltage source is connected to the secondary of the transformer and is raised in steps, while the current value is recorded at each step.
When saturation is reached, the given voltage changes cause much smaller changes in current. The saturation test is used in conjunction with the burden test to make sure that the CT is capable of operating the load (usually protective relays) to which it may be subjected.
If the burden on the CT is too high, it may go into saturation and be unable to maintain its proper ratio. When this happens, protective relays may trip too slowly or not at all due to an insufficient level of current from the CT secondary.
LOW VOLTAGE CIRCUIT BREAKER TESTING BASIC INFORMATION AND TUTORIALS
What test to conduct for low voltage circuit breaker?
Low-voltage circuit breakers come in the following three major types:
a) Power (air-frame) circuit breakers;
b) Molded-case circuit breakers;
c) Insulated-case circuit breakers.
Power circuit breakers start with a frame size of 600 A and go up to 4000 A. The sensing unit that operates the breaker on a short circuit or overload may be either an oil-dash pot with springs and copper coils (for older breakers) or may consist of current transformers (CT) and an electronic trip unit.
With the advent of the electronic trip unit, the number of possible settings and trip functions has dramatically increased, making it easier to coordinate circuit breakers with other protective devices.
Molded-case circuit breakers and insulated-case circuit breakers are very similar in mechanical construction and insulation. The circuit breakers' contacts and operating mechanisms are totally enclosed in a molded plastic housing.
The difference between the two is that a molded-case circuit breaker normally has a thermal-magnetic trip unit (i.e., a trip unit made up of two pieces: a thermal unit to sense overload that uses two dissimilar metals and a magnetic unit to trip on short circuit), while an insulated-case circuit breaker has CTs and an electronic trip unit built into the insulated case.
The most thorough test for all three types of circuit breakers is by "primary injection". A special test set that puts out high (fault level) current at low voltage (typically 6-20 V ac) is used to functionally test the circuit breaker.
These test sets have built-in timing functions; therefore, the breaker can be tested at various currents in order to make sure that it operates within the time-current specifications that are provided by the manufacturer and that it is calibrated to perform in conformance with the coordination study.
For circuit breakers that have electronic trip units, it is often possible to do "secondary injection" testing. This is usually done with a special test set that is designed for the trip unit.
It injects low-level test currents into the trip unit, directly testing only the trip unit. For this reason, primary injection testing is a better practice, as it tests the whole circuit breaker (CTs, shunt trip, etc.) in a manner that is similar to how the breaker would operate during a fault.
In addition to testing the tripping characteristics of the circuit breaker by injecting current, it is also normal practice to test the insulation resistance (usually at 1000 V dc) and the resistance of the breaker's contacts. The contact resistance can be measured directly with a low resistance ohmmeter (usually in milliohms) or indirectly by performing a millivolt drop test.
A millivolt drop test is performed by using a primary injection test set to inject rated continuous current through the breaker while measuring the millivolt drop across the breaker's poles. It is a comparative test between each phase of the breaker in which the millivolt reading typically should not differ by more than 50% between phases.
Power circuit breakers have mechanical adjustments and inspections that should also be periodically checked. The manufacturer's instructions list the adjustments for each model.
Low-voltage circuit breakers come in the following three major types:
a) Power (air-frame) circuit breakers;
b) Molded-case circuit breakers;
c) Insulated-case circuit breakers.
Power circuit breakers start with a frame size of 600 A and go up to 4000 A. The sensing unit that operates the breaker on a short circuit or overload may be either an oil-dash pot with springs and copper coils (for older breakers) or may consist of current transformers (CT) and an electronic trip unit.
With the advent of the electronic trip unit, the number of possible settings and trip functions has dramatically increased, making it easier to coordinate circuit breakers with other protective devices.
Molded-case circuit breakers and insulated-case circuit breakers are very similar in mechanical construction and insulation. The circuit breakers' contacts and operating mechanisms are totally enclosed in a molded plastic housing.
The difference between the two is that a molded-case circuit breaker normally has a thermal-magnetic trip unit (i.e., a trip unit made up of two pieces: a thermal unit to sense overload that uses two dissimilar metals and a magnetic unit to trip on short circuit), while an insulated-case circuit breaker has CTs and an electronic trip unit built into the insulated case.
The most thorough test for all three types of circuit breakers is by "primary injection". A special test set that puts out high (fault level) current at low voltage (typically 6-20 V ac) is used to functionally test the circuit breaker.
These test sets have built-in timing functions; therefore, the breaker can be tested at various currents in order to make sure that it operates within the time-current specifications that are provided by the manufacturer and that it is calibrated to perform in conformance with the coordination study.
For circuit breakers that have electronic trip units, it is often possible to do "secondary injection" testing. This is usually done with a special test set that is designed for the trip unit.
It injects low-level test currents into the trip unit, directly testing only the trip unit. For this reason, primary injection testing is a better practice, as it tests the whole circuit breaker (CTs, shunt trip, etc.) in a manner that is similar to how the breaker would operate during a fault.
In addition to testing the tripping characteristics of the circuit breaker by injecting current, it is also normal practice to test the insulation resistance (usually at 1000 V dc) and the resistance of the breaker's contacts. The contact resistance can be measured directly with a low resistance ohmmeter (usually in milliohms) or indirectly by performing a millivolt drop test.
A millivolt drop test is performed by using a primary injection test set to inject rated continuous current through the breaker while measuring the millivolt drop across the breaker's poles. It is a comparative test between each phase of the breaker in which the millivolt reading typically should not differ by more than 50% between phases.
Power circuit breakers have mechanical adjustments and inspections that should also be periodically checked. The manufacturer's instructions list the adjustments for each model.
PROTECTIVE RELAY TESTING BASIC INFORMATION AND TUTORIALS
What is protective relay testing? How to do protective relay testing?
Protective relaying is a very broad subject. Only a brief overview can be given here. There are two major objectives in protective relaying.
First, a protective relay serves to provide equipment protection (i.e., locate and isolate overloads, short circuits, undervoltages, and other types of electrical problems quickly in order to minimize damage).
Second, the protective device that is closest to the problem should operate first to clear the problem, and no other device should operate unless the closest one fails. This concept, known as "selective tripping" or "selectivity", maintains service to as much of the electrical system as possible by isolating only the problem area.
In order to achieve these objectives, each relay must function as it was designed, and the relays must function in conjunction with the other protective devices in the system. Having all the protective devices function as one overall protective system is called "coordination".
Each protective device has specific parameters within which it has been designed to operate. For example, a single element fuse has a value of current above which it opens.
It takes a specific amount of time for a given current to melt the link away and open the fuse. Manufacturers of fuses publish "time-current" curves that show how long it takes a fuse to operate for varying current values.
Generally, the higher the current, the shorter the time.
This same inverse current-vs.-time concept is used for overcurrent relays and for low-voltage circuit breakers. Relays and low-voltage circuit breakers (with internal trip units) have a range of "pickup" operating current that causes them to operate.
In many cases, this value of current is adjustable. By properly selecting the type, characteristic, and/or setting of fuses, relays, or circuit breakers, the system can be coordinated so that the device that is closest to the problem opens before any device upstream of it. It is necessary to select compatible time current characteristics of the devices for the entire system, in addition to selecting the proper settings for the devices.
Prior to performing protective relay testing, a coordination study should be completed to determine the proper settings for the relays to be calibrated. This is usually done by the design engineer when the system is first installed. If there have been revisions or additions to the system, a new study may be necessary.
Once the coordination study has been completed, the relays need to be calibrated to the proper settings. There are special test sets available for this purpose that inject currents and voltages, as necessary, and time the various operations of the relays.
This type of testing is usually performed by a technician who specializes in this area. Depending upon the relay to be calibrated, quite complex test equipment may be required and in-depth training in protective relaying may be needed to properly set the relay.
Protective relaying is a very broad subject. Only a brief overview can be given here. There are two major objectives in protective relaying.
First, a protective relay serves to provide equipment protection (i.e., locate and isolate overloads, short circuits, undervoltages, and other types of electrical problems quickly in order to minimize damage).
Second, the protective device that is closest to the problem should operate first to clear the problem, and no other device should operate unless the closest one fails. This concept, known as "selective tripping" or "selectivity", maintains service to as much of the electrical system as possible by isolating only the problem area.
In order to achieve these objectives, each relay must function as it was designed, and the relays must function in conjunction with the other protective devices in the system. Having all the protective devices function as one overall protective system is called "coordination".
Each protective device has specific parameters within which it has been designed to operate. For example, a single element fuse has a value of current above which it opens.
It takes a specific amount of time for a given current to melt the link away and open the fuse. Manufacturers of fuses publish "time-current" curves that show how long it takes a fuse to operate for varying current values.
Generally, the higher the current, the shorter the time.
This same inverse current-vs.-time concept is used for overcurrent relays and for low-voltage circuit breakers. Relays and low-voltage circuit breakers (with internal trip units) have a range of "pickup" operating current that causes them to operate.
In many cases, this value of current is adjustable. By properly selecting the type, characteristic, and/or setting of fuses, relays, or circuit breakers, the system can be coordinated so that the device that is closest to the problem opens before any device upstream of it. It is necessary to select compatible time current characteristics of the devices for the entire system, in addition to selecting the proper settings for the devices.
Prior to performing protective relay testing, a coordination study should be completed to determine the proper settings for the relays to be calibrated. This is usually done by the design engineer when the system is first installed. If there have been revisions or additions to the system, a new study may be necessary.
Once the coordination study has been completed, the relays need to be calibrated to the proper settings. There are special test sets available for this purpose that inject currents and voltages, as necessary, and time the various operations of the relays.
This type of testing is usually performed by a technician who specializes in this area. Depending upon the relay to be calibrated, quite complex test equipment may be required and in-depth training in protective relaying may be needed to properly set the relay.
MEDIUM AND HIGH VOLTAGE CABLE TESTING BASIC INFORMATION AND TUTORIALS
Most cables that are rated for use at voltage levels above 600 V are shielded cables. A shielded cable has a conductor in the center, a semiconducting layer over the strands that is surrounded by insulation, a semiconducting layer, and then a metal foil or wire mesh that surrounds the whole assembly.
There is usually another layer over the shield that makes up the outer jacket of the cable. It is a common practice to hi-pot test the cables on initial installation in order to verify that the cables were not damaged when they were pulled into place and that all the splices and/or terminations were installed properly.
The voltage level that is selected usually is lower than factory test levels, frequently 80% of the dc equivalent of the factory test level.
There are normally two considerations that are given to hi-pot testing of cables as a routine maintenance practice. One is a function of the chosen maintenance philosophy [i.e., breakdown maintenance, preventive maintenance, predictive maintenance, or reliability-centered maintenance (RCM)].
The other depends upon the type of operation and how critical it is to have continuous power without interruption.
The debate on whether or not to perform maintenance hi-pot testing centers around the fact that a cable in marginal condition can be caused to fail by the hi-pot test itself. A cable that is in good condition should not be harmed.
People who subscribe to maintenance testing feel that it is much better to have the cable fail under test. Cable maintenance testing frequently is performed at 50-65% of the factory test voltage.
Problems can then be corrected while the circuit is intentionally shut down, thus avoiding an in-service failure that could interrupt production.
It is important to remember that the necessary material, such as splice kits or cable terminations, should be available to facilitate repairs should the cable fail during testing.
There is usually another layer over the shield that makes up the outer jacket of the cable. It is a common practice to hi-pot test the cables on initial installation in order to verify that the cables were not damaged when they were pulled into place and that all the splices and/or terminations were installed properly.
The voltage level that is selected usually is lower than factory test levels, frequently 80% of the dc equivalent of the factory test level.
There are normally two considerations that are given to hi-pot testing of cables as a routine maintenance practice. One is a function of the chosen maintenance philosophy [i.e., breakdown maintenance, preventive maintenance, predictive maintenance, or reliability-centered maintenance (RCM)].
The other depends upon the type of operation and how critical it is to have continuous power without interruption.
The debate on whether or not to perform maintenance hi-pot testing centers around the fact that a cable in marginal condition can be caused to fail by the hi-pot test itself. A cable that is in good condition should not be harmed.
People who subscribe to maintenance testing feel that it is much better to have the cable fail under test. Cable maintenance testing frequently is performed at 50-65% of the factory test voltage.
Problems can then be corrected while the circuit is intentionally shut down, thus avoiding an in-service failure that could interrupt production.
It is important to remember that the necessary material, such as splice kits or cable terminations, should be available to facilitate repairs should the cable fail during testing.
HIGH POTENTIAL (HI POT) TESTING BASIC INFORMATION AND TUTORIALS
What is HiPot testing?
High-potential testing, as its name implies, utilizes higher levels of voltage in performing the tests. It is generally utilized on medium-voltage (1000Ð69 000 V) and on high-voltage (above 69 000 V) equipment.
As stated earlier, the leakage current is usually measured. In some cases, such as in cable hi-potting, the value of leakage current is significant and can be used analytically. In other applications, such as switchgear hi-potting, it is a pass/fail type of test, in which sustaining the voltage level for the appropriate time (usually 1 min) is considered "passing."
High-potential testing, as its name implies, utilizes higher levels of voltage in performing the tests. It is generally utilized on medium-voltage (1000Ð69 000 V) and on high-voltage (above 69 000 V) equipment.
As stated earlier, the leakage current is usually measured. In some cases, such as in cable hi-potting, the value of leakage current is significant and can be used analytically. In other applications, such as switchgear hi-potting, it is a pass/fail type of test, in which sustaining the voltage level for the appropriate time (usually 1 min) is considered "passing."
INSULATION RESISTANCE TEST BASIC INFORMATION AND TUTORIALS
What is insulation resistance test? How to conduct insulation resistance test?
Insulation resistance tests are typically performed on motors, circuit breakers, transformers, low-voltage (unshielded) cables, switchboards, and panel boards to determine if degradation due to aging, environmental, or other factors has affected the integrity of the insulation.
This test is normally conducted for 1 min, and the insulation resistance value is then recorded. As mentioned earlier, the electrical properties of the insulation and the amount of surface area directly affect the capacitance between the conductor and ground, and therefore affect the charging time.
With larger motors, generators, and transformers, a common test is to measure the "dielectric absorption ratio" or the "polarization index" of the piece of equipment being tested. The dielectric absorption ratio is the 1 min insulation resistance reading divided by the 30 s insulation resistance reading.
The polarization index is the 10 min (continuous) insulation resistance reading divided by the 1 min reading. Both of these provide additional information as to the quality of the insulation.
Many types of insulation become dry and brittle as they age, thereby becoming less effective capacitors. Thus, a low polarization index (less than 2.0) may indicate poor insulation.
Even though insulation may have a high insulation resistance reading, there could still be a problem, since the motor and transformer windings are subjected to strong mechanical stresses on starting. With the exception of electronic equipment (which can be damaged by testing), insulation resistance testing is normally done on most types of new equipment and is also part of a maintenance program.
It is a good practice to perform insulation resistance testing on switchgear and panelboards after maintenance has been performed on them, just prior to re-energizing them. This prevents re-energizing the equipment with safety grounds still applied or with tools accidentally left inside.
Insulation resistance tests are typically performed on motors, circuit breakers, transformers, low-voltage (unshielded) cables, switchboards, and panel boards to determine if degradation due to aging, environmental, or other factors has affected the integrity of the insulation.
This test is normally conducted for 1 min, and the insulation resistance value is then recorded. As mentioned earlier, the electrical properties of the insulation and the amount of surface area directly affect the capacitance between the conductor and ground, and therefore affect the charging time.
With larger motors, generators, and transformers, a common test is to measure the "dielectric absorption ratio" or the "polarization index" of the piece of equipment being tested. The dielectric absorption ratio is the 1 min insulation resistance reading divided by the 30 s insulation resistance reading.
The polarization index is the 10 min (continuous) insulation resistance reading divided by the 1 min reading. Both of these provide additional information as to the quality of the insulation.
Many types of insulation become dry and brittle as they age, thereby becoming less effective capacitors. Thus, a low polarization index (less than 2.0) may indicate poor insulation.
Even though insulation may have a high insulation resistance reading, there could still be a problem, since the motor and transformer windings are subjected to strong mechanical stresses on starting. With the exception of electronic equipment (which can be damaged by testing), insulation resistance testing is normally done on most types of new equipment and is also part of a maintenance program.
It is a good practice to perform insulation resistance testing on switchgear and panelboards after maintenance has been performed on them, just prior to re-energizing them. This prevents re-energizing the equipment with safety grounds still applied or with tools accidentally left inside.
CREATING AND ELECTRICAL PREVENTIVE MAINTENANCE PROGRAM BASIC TUTORIALS
Preparing a preventive maintenance program basic information
To be successful, a preventive maintenance program shall have the backing of management. There should be the belief that operating profit is increased through the judicious spending of maintenance dollars. Financial issues should be considered when evaluating the need for continuous electrical power.
These factors will help to dictate the level of importance that a facility places on a preventive maintenance program. The cost of downtime or lost production, and how that can be minimized through effective maintenance, also should be considered.
A complete survey of the plant should be performed. This survey should include a listing of all electrical equipment and systems. The equipment should be listed in a prioritized fashion in order to distinguish those systems or pieces of equipment that are most critical to the operation.
The survey should also include a review of the status of drawings, manuals, maintenance logs, safety and operating procedures, and training and other appropriate records. It should be recognized that the survey itself can be a formidable task.
It is likely that power outages may be required in order to complete the survey. The gathering of documentation is important. This includes not only the drawings of the facilities, but also all the documentation that is normally provided by the manufacturer of the equipment.
The manufacturer's manuals should include recommended maintenance procedures, wiring diagrams, bills of materials, assembly and operating instructions, and troubleshooting recommendations.
Next, the necessary procedures for maintaining each item on the list should be developed. NFPA 70B-1994 [B3] and NETA MTS-1993 [B2] are valuable resources that provide much of this information. Procedures should also be developed that integrate the equipment into systems. People that are capable of performing the procedures should be selected and trained. At some level of technical performance, it may be desirable to contract parts of the maintenance program to qualified outside firms, particularly those functions that require special test equipment to perform.
Finally, a process shall be developed to administer the program. This process may be manual or software-based. There are many commercially available systems with varying levels of sophistication.
Consideration also shall be given to some of the less technical parts of the process. Pre-maintenance considerations might include the logistics of getting equipment in and out of the area to be maintained, general safety procedures, procedures to be followed in the event of an emergency, and record-keeping that has to be accomplished ahead of the maintenance activity, as well as follow-up maintenance, special lighting needs, and equipment-specific safety precautions.
In addition, an ongoing task is that of keeping access to electrical equipment free from being blocked by stored materials, such as spare parts. Record keeping and maintenance follow-up activities also shall be considered.
To be successful, a preventive maintenance program shall have the backing of management. There should be the belief that operating profit is increased through the judicious spending of maintenance dollars. Financial issues should be considered when evaluating the need for continuous electrical power.
These factors will help to dictate the level of importance that a facility places on a preventive maintenance program. The cost of downtime or lost production, and how that can be minimized through effective maintenance, also should be considered.
A complete survey of the plant should be performed. This survey should include a listing of all electrical equipment and systems. The equipment should be listed in a prioritized fashion in order to distinguish those systems or pieces of equipment that are most critical to the operation.
The survey should also include a review of the status of drawings, manuals, maintenance logs, safety and operating procedures, and training and other appropriate records. It should be recognized that the survey itself can be a formidable task.
It is likely that power outages may be required in order to complete the survey. The gathering of documentation is important. This includes not only the drawings of the facilities, but also all the documentation that is normally provided by the manufacturer of the equipment.
The manufacturer's manuals should include recommended maintenance procedures, wiring diagrams, bills of materials, assembly and operating instructions, and troubleshooting recommendations.
Next, the necessary procedures for maintaining each item on the list should be developed. NFPA 70B-1994 [B3] and NETA MTS-1993 [B2] are valuable resources that provide much of this information. Procedures should also be developed that integrate the equipment into systems. People that are capable of performing the procedures should be selected and trained. At some level of technical performance, it may be desirable to contract parts of the maintenance program to qualified outside firms, particularly those functions that require special test equipment to perform.
Finally, a process shall be developed to administer the program. This process may be manual or software-based. There are many commercially available systems with varying levels of sophistication.
Consideration also shall be given to some of the less technical parts of the process. Pre-maintenance considerations might include the logistics of getting equipment in and out of the area to be maintained, general safety procedures, procedures to be followed in the event of an emergency, and record-keeping that has to be accomplished ahead of the maintenance activity, as well as follow-up maintenance, special lighting needs, and equipment-specific safety precautions.
In addition, an ongoing task is that of keeping access to electrical equipment free from being blocked by stored materials, such as spare parts. Record keeping and maintenance follow-up activities also shall be considered.
ELECTRIC POWER UTILITY OPERATING ECONOMICS BASICS
It is important to operate an electrical distribution system economically because of the high costs of losses and the cost of system expansion. Today, there are numerous methods for monitoring and controlling the power flow through the distribution system.
These methods range from simple ammeter, voltmeter, wattmeter, and varmeter systems to complex supervisory control and data acquisition systems. A system can be designed to fit the needs and budget of any size facility.
Energy conservation
Energy conservation is the key to the economic operation of a power system, regardless of the methods that are used to monitor and control the energy flow through the system. Energy conservation begins with thorough and complete design practices. The system should be operated in such a manner as to keep losses to a minimum and to minimize any utility power factor or demand charges.
Power-factor correction
Power-factor correction, by the addition of capacitors at the facility service point, reduces power-factor charges from the serving utility. This, however, does not release any capacity of the load-side distribution system.
Power-factor correction, closer to the loads, reduces currents in the main feeder conductors. This reduces the system losses, reduces power-factor billing charges, releases circuit capacity, and improves voltage regulation. The release of circuit capacity may be used to avoid costly system expansion projects by allowing additional circuit loading.
Utility demand charge
Most utilities have a demand charge that is based on kilovolt-amperes and kilowatts, or kilovolt-ampere-hours and kilowatt-hours, which automatically includes power factor, and they charge a financial penalty for loads that operate below a specified minimum power factor.
The demand level is dependent upon the type of industrial plant or commercial facility. The system operator should develop the logic of that operation so that effective demand control can be practiced.
Demand charges normally are maintained at peak levels for finite time periods after a new peak is established. The cost of a single peaking event could have a recurring cost for as long as 12 months.
Lack of demand control can escalate one apparently small indiscretion into a very expensive event. The unnecessary operation of spare equipment that adds load to the system, even for a short time, should be avoided so as not to increase demand peaks.
The operator should be aware of the serving utility rate/demand structure in order to operate at peak effectiveness and to avoid any unnecessary demand charges.
These methods range from simple ammeter, voltmeter, wattmeter, and varmeter systems to complex supervisory control and data acquisition systems. A system can be designed to fit the needs and budget of any size facility.
Energy conservation
Energy conservation is the key to the economic operation of a power system, regardless of the methods that are used to monitor and control the energy flow through the system. Energy conservation begins with thorough and complete design practices. The system should be operated in such a manner as to keep losses to a minimum and to minimize any utility power factor or demand charges.
Power-factor correction
Power-factor correction, by the addition of capacitors at the facility service point, reduces power-factor charges from the serving utility. This, however, does not release any capacity of the load-side distribution system.
Power-factor correction, closer to the loads, reduces currents in the main feeder conductors. This reduces the system losses, reduces power-factor billing charges, releases circuit capacity, and improves voltage regulation. The release of circuit capacity may be used to avoid costly system expansion projects by allowing additional circuit loading.
Utility demand charge
Most utilities have a demand charge that is based on kilovolt-amperes and kilowatts, or kilovolt-ampere-hours and kilowatt-hours, which automatically includes power factor, and they charge a financial penalty for loads that operate below a specified minimum power factor.
The demand level is dependent upon the type of industrial plant or commercial facility. The system operator should develop the logic of that operation so that effective demand control can be practiced.
Demand charges normally are maintained at peak levels for finite time periods after a new peak is established. The cost of a single peaking event could have a recurring cost for as long as 12 months.
Lack of demand control can escalate one apparently small indiscretion into a very expensive event. The unnecessary operation of spare equipment that adds load to the system, even for a short time, should be avoided so as not to increase demand peaks.
The operator should be aware of the serving utility rate/demand structure in order to operate at peak effectiveness and to avoid any unnecessary demand charges.
POWER SYSTEM PROTECTION COORDINATION FOR SAFETY
When an electrical distribution system is designed and constructed, a fault-current coordination study should be conducted, and circuit protective devices should be sized and set according to the results of the study. In time, however, the electrical system configurations are often changed due to the changing needs of the end users.
If the coordination and capability of the electrical equipment are not reviewed at the time of the changes, faults could result in unnecessary tripping of a main breaker or, even worse, an explosion of equipment that was thought to be in good condition.
When system conditions change, the results that were obtained in the original fault-current coordination study may no longer apply to the current system. Unnecessary tripping, known as lack of selectivity, could be caused by poor coordination.
An equipment explosion could result from the interrupting capability of the circuit breaker being exceeded. Both indicate a clear need for an updated fault-current coordination study.
Utility systems delivering higher fault currents
The demand for electricity, particularly in the industrial and commercial environment, has been steadily increasing. Consequently, utility systems have grown much larger and have become capable of delivering much higher fault-currents at service points than in the past.
Therefore, protective devices that were properly applied at the time they were installed may have become inadequate after system changes, and the protective system may no longer be coordinated. When available fault current increases to the point at which it exceeds protective device interrupting and withstand ratings, violent failure is possible, regardless of how well the devices are maintained.
Protection in an electrical distribution system
System and equipment protective devices are a form of insurance. This insurance pays nothing as long as there is no fault or other emergency.
When a fault occurs, however, properly applied protective devices reduce the extent and duration of the interruption, thereby reducing the exposure to personal injury and property damage. If, however, the protective system does not match system needs, just as an insurance policy should keep up with inflation, it is no help at all. It is the responsibility of the system operator to ensure proper system protection and coordination.
Protective equipment set to sense and remove short circuits
In medium-voltage systems, the protective equipment for feeder conductors is often set to sense and remove short circuits, but not necessarily to provide overload protection of circuits. Device settings sometimes are purposely chosen low enough to sense and provide a degree of overload protection.
Operators should be aware of this so that a protective device that is set lower than necessary for coordination does not cause a false tripping action during system switching procedures. System protection coordination is an important consideration in switching systems with loop feeds and alternate sources. To avoid false tripping action, operators should be aware of the settings and any probable temporary overloads or circulating currents during switching.
If the coordination and capability of the electrical equipment are not reviewed at the time of the changes, faults could result in unnecessary tripping of a main breaker or, even worse, an explosion of equipment that was thought to be in good condition.
When system conditions change, the results that were obtained in the original fault-current coordination study may no longer apply to the current system. Unnecessary tripping, known as lack of selectivity, could be caused by poor coordination.
An equipment explosion could result from the interrupting capability of the circuit breaker being exceeded. Both indicate a clear need for an updated fault-current coordination study.
Utility systems delivering higher fault currents
The demand for electricity, particularly in the industrial and commercial environment, has been steadily increasing. Consequently, utility systems have grown much larger and have become capable of delivering much higher fault-currents at service points than in the past.
Therefore, protective devices that were properly applied at the time they were installed may have become inadequate after system changes, and the protective system may no longer be coordinated. When available fault current increases to the point at which it exceeds protective device interrupting and withstand ratings, violent failure is possible, regardless of how well the devices are maintained.
Protection in an electrical distribution system
System and equipment protective devices are a form of insurance. This insurance pays nothing as long as there is no fault or other emergency.
When a fault occurs, however, properly applied protective devices reduce the extent and duration of the interruption, thereby reducing the exposure to personal injury and property damage. If, however, the protective system does not match system needs, just as an insurance policy should keep up with inflation, it is no help at all. It is the responsibility of the system operator to ensure proper system protection and coordination.
Protective equipment set to sense and remove short circuits
In medium-voltage systems, the protective equipment for feeder conductors is often set to sense and remove short circuits, but not necessarily to provide overload protection of circuits. Device settings sometimes are purposely chosen low enough to sense and provide a degree of overload protection.
Operators should be aware of this so that a protective device that is set lower than necessary for coordination does not cause a false tripping action during system switching procedures. System protection coordination is an important consideration in switching systems with loop feeds and alternate sources. To avoid false tripping action, operators should be aware of the settings and any probable temporary overloads or circulating currents during switching.
SAFETY AND POWER SYSTEM MANAGEMENT BASIC INFORMATION AND TUTORIALS
A well designed and constructed power system will not provide a safe and reliable operation unless it is properly managed. Any electrical power distribution system, from the smallest system to the largest and most complex system, needs to be managed. As systems become larger in size and complexity, the problems of system management increase, thereby requiring more time and attention from the system-operating personnel.
Good design, proper installation, quality assurance, and sound operating and maintenance programs provide the basic foundation for the safe and reliable operation of industrial electric power systems. A plant engineer who is faced with the task of improving the plant's electric power system performance, however, will likely find that programs to reduce human error are more cost-effective than system modifications or additional preventive maintenance. In fact, given good design and a sound maintenance program, the inherent system reliability can only be achieved by the reduction of operating error.
The operation of an electric power system should also address the problem of human errors. The following examples should be considered:
Following a severe thunderstorm, a plant shift supervisor made a walk-through inspection of the plant's primary distribution switchgear. Upon seeing a red light for each circuit breaker, he immediately tripped each circuit breaker in order to obtain a green-light indication. Because he incorrectly thought that the red light meant "open," he shut down the entire plant.
One of a plant's two steam boilers was down for annual inspection and maintenance. An electrician who was assigned to make a modification to the boiler control circuit erroneously began working on the operating boiler control circuit and shut down the operating boiler.
An investigation of a 15 kV outdoor bus duct fault revealed that production personnel routinely turned off outside lighting at the beginning of the day shift by switching off circuit breakers in a 120 V distribution panel. The bus duct heater circuit was incorrectly identified, and was being switched off with the lighting circuits.
It is a natural tendency to blame equipment for failures, rather than human error. The bus duct fault in the last example could have been classified as an equipment failure; however, the prime cause was improper operation (human error) of the bus duct heaters.
Most plant electrical outages that clearly are not due to equipment failure, lightning, or utility disturbances can be prevented by making an objective investigation of the potential for outages and by following these guidelines:
a) Document the system and identify the equipment.
b) Plan switching operations in detail.
c) Secure equipment from unintentional operation.
d) Clearly define operating responsibility and adhere to it rigidly. System operation can and should be managed.
Effective managers of a power system will consider load distribution, system integrity, power factor, system protection coordination, and operating economics. Each of these areas is discussed in this chapter, thus showing how all of these considerations relate to each other. No area of industrial and commercial power system management is independent of the other.
Good design, proper installation, quality assurance, and sound operating and maintenance programs provide the basic foundation for the safe and reliable operation of industrial electric power systems. A plant engineer who is faced with the task of improving the plant's electric power system performance, however, will likely find that programs to reduce human error are more cost-effective than system modifications or additional preventive maintenance. In fact, given good design and a sound maintenance program, the inherent system reliability can only be achieved by the reduction of operating error.
The operation of an electric power system should also address the problem of human errors. The following examples should be considered:
Following a severe thunderstorm, a plant shift supervisor made a walk-through inspection of the plant's primary distribution switchgear. Upon seeing a red light for each circuit breaker, he immediately tripped each circuit breaker in order to obtain a green-light indication. Because he incorrectly thought that the red light meant "open," he shut down the entire plant.
One of a plant's two steam boilers was down for annual inspection and maintenance. An electrician who was assigned to make a modification to the boiler control circuit erroneously began working on the operating boiler control circuit and shut down the operating boiler.
An investigation of a 15 kV outdoor bus duct fault revealed that production personnel routinely turned off outside lighting at the beginning of the day shift by switching off circuit breakers in a 120 V distribution panel. The bus duct heater circuit was incorrectly identified, and was being switched off with the lighting circuits.
It is a natural tendency to blame equipment for failures, rather than human error. The bus duct fault in the last example could have been classified as an equipment failure; however, the prime cause was improper operation (human error) of the bus duct heaters.
Most plant electrical outages that clearly are not due to equipment failure, lightning, or utility disturbances can be prevented by making an objective investigation of the potential for outages and by following these guidelines:
a) Document the system and identify the equipment.
b) Plan switching operations in detail.
c) Secure equipment from unintentional operation.
d) Clearly define operating responsibility and adhere to it rigidly. System operation can and should be managed.
Effective managers of a power system will consider load distribution, system integrity, power factor, system protection coordination, and operating economics. Each of these areas is discussed in this chapter, thus showing how all of these considerations relate to each other. No area of industrial and commercial power system management is independent of the other.
WIRE SIZES AMERICAN WIRE GAGE (AWG) FORMER BROWNE & SHARPE
Wire Sizes
In the United States, it is common practice to indicate wire sizes by gage numbers. The source of these numbers for electrical wire is the American Wire Gage (AWG) (otherwise known as the Brown & Sharpe Gage).
A small wire is designated by a large number and a large wire by a small number as shown in below.
The diameter of a No. 0000 wire is 0.4600 inch or 460 mils; the diameter of a No. 36 wire is 0.0050 inch or 5 mils. There are 38 other sizes between these two extremes. For example, a No. 8 wire is 0. 1285 inch (128.5 mils) in diameter and a No. 1 wire is 0.2576 (257.6 mils) in diameter.
It has proved convenient to discuss the cross-section area of a wire in circular mils. A circular mil (cm) is the area of a circle having a diameter of 0.001 inch or 1 mil. Because it is a circular area unit of measure, it is necessary only to square the number of mils given in the diameter of a wire to find the number of circular mils in a circle of that diameter.
Thus, a conductor with a 1-mil diameter would have a 1-circular-mil (cm) cross-section area; a 3-mil diameter wire would have a 9-cm area; and a 40-mil-diameter wire, a 1600-cm area.
For conductors larger than 0000 (4/0) in size, the wire sizes are expressed in circular mils; for example, 350,000 cm, 500,000 cm, and so on. (Sometimes these are expressed as 350 mcm, 500 mcm, etc.)
In the United States, it is common practice to indicate wire sizes by gage numbers. The source of these numbers for electrical wire is the American Wire Gage (AWG) (otherwise known as the Brown & Sharpe Gage).
A small wire is designated by a large number and a large wire by a small number as shown in below.
The diameter of a No. 0000 wire is 0.4600 inch or 460 mils; the diameter of a No. 36 wire is 0.0050 inch or 5 mils. There are 38 other sizes between these two extremes. For example, a No. 8 wire is 0. 1285 inch (128.5 mils) in diameter and a No. 1 wire is 0.2576 (257.6 mils) in diameter.
It has proved convenient to discuss the cross-section area of a wire in circular mils. A circular mil (cm) is the area of a circle having a diameter of 0.001 inch or 1 mil. Because it is a circular area unit of measure, it is necessary only to square the number of mils given in the diameter of a wire to find the number of circular mils in a circle of that diameter.
Thus, a conductor with a 1-mil diameter would have a 1-circular-mil (cm) cross-section area; a 3-mil diameter wire would have a 9-cm area; and a 40-mil-diameter wire, a 1600-cm area.
For conductors larger than 0000 (4/0) in size, the wire sizes are expressed in circular mils; for example, 350,000 cm, 500,000 cm, and so on. (Sometimes these are expressed as 350 mcm, 500 mcm, etc.)
ELECTRIC RESISTANCE HEATERS BASIC INFORMATION AND TUTORIALS

These common devices carry the disadvantage of using high-grade energy to do a low-grade task. Their advantages, however, are impressive: low first cost and individual thermostatic control that can easily be used to make each room a separate heating zone.
Thus, the energy wasted at the electricity-generating plant (usually 60% to 70%) can be partially “recovered” at the building, where unused rooms can remain unheated.
As in the case of metal wood stoves, surfaces can sometimes reach high temperatures, requiring care in the location of heaters relative to furniture placement, draperies, and traffic flow.
Electric heaters are sized by their capacity in kilowatts (1 kW = 3413 Btu/h). The maximum watt density allowed is 250 W per linear foot of heater (820 W per linear meter).
HOTLINE TOOLS SAFETY RULES BASIC INFORMATION AND TUTORIALS
What are the safety rules in using hotline tools?

Follow these safety rules when working with hot-line tools:
• Do not perform hot-line work when rain or snow is threatening or when heavy dew, fog, or other excessive moisture is present. Exceptions to this rule are when conducting switching operations, fusing, or clearing damaged equipment that presents a hazard to the public or to troops.
• Remain alert. If rain or snow starts to fall or an electrical storm appears while a job is in progress, complete the work as quickly as possible to allow safe, temporary operation of the line until precipitation or lightning ceases. Judgment of safe weather conditions for hot-line work is the foreman's responsibility.
• Perform hot-line work during daylight if possible. In emergency situations, work under artificial light if all conductors and equipment being worked on are made clearly visible.
• Do not wear rubber gloves with hot-line tools because they make detection of brush discharges impossible.
• Avoid holding outer braces or other metal attachments.
• Avoid unnecessary conversation.
• Maintain close cooperation among everyone on the job.
• Treat wooden pole structures the same as steel towers.
• Be careful with distribution primaries. When they are located on the same pole with high-tension lines, cover them with rubber protective equipment before climbing through or working above them.
• Do not change your position on the pole without first looking around and informing others.
• Never use your hands to hold a live line clear of a lineman on a pole. Secure the line with live-line tools and
lock it in a clamp.
• Stay below the live wire when moving it until it is thoroughly secured in a safe working position.
• Take special precautions on poles having guy lines.
• Do not use a rope on conductors carrying more than 5,000 volts unless the rope is insulated from the conductor with an insulated tension link stick.
Follow these safety rules when working with hot-line tools:
• Do not perform hot-line work when rain or snow is threatening or when heavy dew, fog, or other excessive moisture is present. Exceptions to this rule are when conducting switching operations, fusing, or clearing damaged equipment that presents a hazard to the public or to troops.
• Remain alert. If rain or snow starts to fall or an electrical storm appears while a job is in progress, complete the work as quickly as possible to allow safe, temporary operation of the line until precipitation or lightning ceases. Judgment of safe weather conditions for hot-line work is the foreman's responsibility.
• Perform hot-line work during daylight if possible. In emergency situations, work under artificial light if all conductors and equipment being worked on are made clearly visible.
• Do not wear rubber gloves with hot-line tools because they make detection of brush discharges impossible.
• Avoid holding outer braces or other metal attachments.
• Avoid unnecessary conversation.
• Maintain close cooperation among everyone on the job.
• Treat wooden pole structures the same as steel towers.
• Be careful with distribution primaries. When they are located on the same pole with high-tension lines, cover them with rubber protective equipment before climbing through or working above them.
• Do not change your position on the pole without first looking around and informing others.
• Never use your hands to hold a live line clear of a lineman on a pole. Secure the line with live-line tools and
lock it in a clamp.
• Stay below the live wire when moving it until it is thoroughly secured in a safe working position.
• Take special precautions on poles having guy lines.
• Do not use a rope on conductors carrying more than 5,000 volts unless the rope is insulated from the conductor with an insulated tension link stick.
SELECTION OF LINEMAN ELECTRICAL PROTECTIVE EQUIPMENT BASIC INFORMATION AND TUTORIALS
How to select electrical protective equipment for lineman safety engineering?

The requirements for the hazard analysis and selection of protective clothing must first be defined.
Assess the workplace to determine if hazards are present, or are likely to be present, which require the use of personal protective equipment. If such hazards are determined, the employer should select and have each employee use, the type of personal productive equipment that will protect the affected employee from the hazards identified in the hazard assessment.
Train the employee to be knowledgeable with the following issues and scenarios:
• When personal productive equipment is necessary;
• What personal productive equipment is necessary;
• How to properly don, doff, adjust, and wear personal productive equipment;
• The limitations of the personal productive equipment;
and
• The proper care, maintenance, useful life, and disposal of personal productive equipment.
Include shock, arc, and blast assessments in the hazard analyses. Identify the selection, inspection, and use requirements for electrical personal productive equipment. Specify the type of clothing that is prohibited.
Utilize protective shields, protective barriers, or insulating materials to protect each employee from shock, burns, or other electrically related injuries while that employee is working near exposed energized parts which might be accidentally contacted or where dangerous electric heating or arcing might occur.
Protective clothing, including a complete multilayered flash suit with hood and face shield, may be required for the operation, insertion, or removal of a circuit breaker.
Calculate the incident energy (in cal/cm2) available at the work site in order to determine and the protective clothing required for the specific task. Additionally, determine a "Flash protection boundary" for all energized work.
At this boundary, exposed flesh must not receive a second-degree burn or worse. After determining the type, purchase the necessary protective
clothing and train employees on how to properly wear the gear.
The requirements for the hazard analysis and selection of protective clothing must first be defined.
Assess the workplace to determine if hazards are present, or are likely to be present, which require the use of personal protective equipment. If such hazards are determined, the employer should select and have each employee use, the type of personal productive equipment that will protect the affected employee from the hazards identified in the hazard assessment.
Train the employee to be knowledgeable with the following issues and scenarios:
• When personal productive equipment is necessary;
• What personal productive equipment is necessary;
• How to properly don, doff, adjust, and wear personal productive equipment;
• The limitations of the personal productive equipment;
and
• The proper care, maintenance, useful life, and disposal of personal productive equipment.
Include shock, arc, and blast assessments in the hazard analyses. Identify the selection, inspection, and use requirements for electrical personal productive equipment. Specify the type of clothing that is prohibited.
Utilize protective shields, protective barriers, or insulating materials to protect each employee from shock, burns, or other electrically related injuries while that employee is working near exposed energized parts which might be accidentally contacted or where dangerous electric heating or arcing might occur.
Protective clothing, including a complete multilayered flash suit with hood and face shield, may be required for the operation, insertion, or removal of a circuit breaker.
Calculate the incident energy (in cal/cm2) available at the work site in order to determine and the protective clothing required for the specific task. Additionally, determine a "Flash protection boundary" for all energized work.
At this boundary, exposed flesh must not receive a second-degree burn or worse. After determining the type, purchase the necessary protective
clothing and train employees on how to properly wear the gear.
Subscribe to:
Posts (Atom)